
By selecting an indicator of your interest, information will be displayed below:
General Indicators
Corporate Governance
Corporate Profile
Ethics and Integrity
Reporting practice
Stakeholder engagement
Strategy
Material Topics
Business development and Economic performance
Climate Change Risk Management
Commitment and Working Environment
Community Engagement
Customer Health and Safety
Environmental Management and Operating Efficiency
Ethics and anticorruption
Innovation in products and processes
Occupational Health and Safety
Supply Chain Management
417-3. Incidents of non-compliance concerning marketing communications
This year, one incident of non-compliance with marketing communications was reported, due to the placement of suspension stamps in three advertising locations for McCormick brand teas. The advertising was withdrawn from all the hoardings and the authority issued a single minor penalty.
417-1. Requirements for product and service information and labeling
Our labels are the main form of communicating the most important information about our products to our customers. This information includes the origin of the product's components, nutritional information—especially saturated fats, sugars, sodium and calorie content—net content, safety instructions and the best way to dispose of or recycle the packaging. We make an exhaustive inspection of the ingredients that go into our different products to ensure they comply with the applicable regulations, both locally and, where appropriate, in the country to which they are exported.
Labeling, as such, is not directly related to environmental or social impact, but there are other procedures for withdrawing a product from the market which address that situation. All our labels meet the regulations applicable in the country of destination. In the case of Mexico, all are designed in accordance with Sanitary Control Regulations for products, NOM-050-SCFI-2004: Commercial Information; General Product Labeling and NOM-051-SCFI/SSA1-2010: General labeling specifications for pre-packaged food and non-alcoholic beverages-Commercial and sanitary information.
416-2. Incidents of non-compliance concerning the health and safety impacts of products and services
During 2018, 1 case was presented regarding the health and safety of our products.
At our Galerías Atizapán, Estado de México branch, product was immobilized for having expired. A non-significant penalty was paid.
103-5. Management Approach
Our broad portfolio of brands and strict parameters on quality and harmlessness promote a healthy lifestyle for our clients and consumers. Our labeling, based on the best national and international practices, communicates graphically and effectively the nutritional content and energy contribution of each of our products, enabling our customers and consumers to make informed decisions.
103-11. Management Approach
Through the unification of strategies and continuous improvement processes, managed by the Environmental Control, Safety and Hygiene (CASH for its initials in Spanish) area, we safeguard the integrity and wellbeing of our employees; we prevent and mitigate incidents that affect the environment, and maintain a culture of safety and risk prevention, thereby ensuring the continuity of our operations.
Our Industrial Safety Policy can be found at https://grupoherdez.com.mx/sustentabilidad/codigos-y-politicas/
103-9. Management approach
Innovation is one of the five strategic pillars upon which we have built sustainable and responsible growth over more than 100 years. A decisive factor in that growth has been the ability to clearly understand the present and future needs of our clients and consumers and provide solutions with unique value through our extensive and growing portfolio of products and services.
Through a continuous creation process and idea-to-launch methodology, our innovation area conceptualizes, develops and markets our products and services, allowing us a culture of disruptive product innovation, to position as customer-focused, high performance leaders and to anticipate and manage market risks and thus transform quickly, profitably and successfully.
The Company stays abreast of the nutritional needs of the national population and international markets, in order to provide increasingly healthier products for consumers.
409-1. Operations and suppliers at significant risk for incidents of forced labor
Our Supplier Code of Conduct contains the minimum requirements for our current and potential suppliers in terms of the social and environmental conditions for the development of their operations and services. The document is based on the standards of the International Labor Organization (ILO), the ten principles of the United Nations Global Compact, and the Human Rights Policy and Code of Ethics of Grupo Herdez, which establishes that Grupo Herdez rejects, without exception, all forms of forced or compulsory labor, any form of child labor for whatever purpose, whether full or part time, including remunerated or otherwise.
408-1. Operations and suppliers at significant risk for incidents of child labor
We maintain strict control over our hiring processes on fishing vessels and have a purchasing policy and supplier code containing clauses that prohibit the hiring of suppliers who employ child labor or forced labor. This measure avoids the risk of employing child labor throughout our value chain, especially in the most vulnerable sectors like agriculture and fishing. The Supplier Code of Conduct can be found at: https://grupoherdez.com.mx/sustentabilidad/codigos-y-politicas/
204-1. Proportion of spending on local suppliers
Grupo Herdez defines local or national suppliers as those with manufacturing and transformation facilities located in Mexican territory.
Raw Materials
Only 8.15 percent of non-perishable raw materials is purchased from foreign suppliers, equivalent to $356,074,738,* the remaining 91.85 percent, equivalent to $4,014,048,610 goes to domestic purchases.
* Soy bean comes under domestic purchases since although its main origin is the United States, the end product--soy oil--is refined in Mexico.
Packaging Material
74.6 percent of total spending on packaging materials goes to domestic suppliers, which is the equivalent of $2,085,519,706.27, 4.1 percent goes to foreign suppliers, the equivalent of $114,788,832.45 and 21.3 percent goes to a mix of domestic and foreign supply, equivalent to $595,293,389.9.
* A large part of the raw packaging materials (resins, special substrates, adhesives, tinplate, among others) is of foreign origin, however, it is transformed in Mexico, particularly the manufacture of pulp and paper for corrugated cardboard. Imported materials are purchased only in the event of shortage.
Agricultural Supply
All our agricultural producers operate in Mexico, with operations throughout the Mexican Republic, in Aguascalientes, Baja California, Baja California Sur, Chihuahua, Mexico City, Durango, Guanajuato, Hidalgo, Morelos, Nayarit, Nuevo León, Puebla, San Luis Potosí, Sinaloa, Sonora and Zacatecas.
In 2018, the purchase of agricultural inputs represented an investment of $823,000,000.
*Figures expressed in Mexican pesos (MXN).
103-3. Management approach
Strategic Supply
Our supply chain consists of all the activities we use to get our products and services onto the tables of clients and consumers with their characteristic reliability and quality. We work under four strategic pillars: utility, innovation, productivity and risk management, an approach which enables us to ensure the supply of necessary resources for our present and future operations and to establish mutually valuable relationships with our suppliers.
Similarly, through the Supply area and by following the guidelines of the Carbon Disclosure Project, we constantly monitor the impact of our consumption of raw materials that are highly vulnerable to environmental and forest risks, such as soy oil, and wood.
Agricultural Supply
Our agricultural supply area is responsible for ensuring the quality and traceability of all our agricultural products. We achieve this along three pillars: supply, supplier development and agricultural auditing.
The care, development and monitoring of all our agricultural suppliers, is key to achieving an efficient and responsible value chain.
415-1. Political contributions
In compliance with our Code of Ethics, which requires a strictly neutral stance in matters of politics and religion, Grupo Herdez and its subsidiaries make no financial and/or in-kind contributions to political parties or related institutions; nor does it receive financial assistance from the government. The Group has an Ethics Committee made up of a team of six members from different areas, who join forces with our directors to provide guidance in favor of ethical and lawful conduct. Our Code of Ethics can be found at: https://grupoherdez.com.mx/sustentabilidad/codigos-y-politicas/
206-1. Legal actions for anti-competitive behavior, anti-trust, and monopoly practices
In 2018, there were no complaints of monopoly or unfair practices. However, despite there being no cases of this kind in recent years, the Anti-trust and Economic Competition Policy was adopted in 2018 and can be found at: https://grupoherdez.com.mx/sustentabilidad/codigos-y-politicas/
205-3. Confirmed incidents of corruption and action taken
Incidents related to non-compliance with the Code of Ethics on topics of corruption and breach of human rights are reported confidentially through the Ética Herdez line. The line is monitored by an external supplier, which periodically shares a consolidated report with the management of Human Resources and the general management of Internal Audit; Internal Audit is responsible for following up and investigating all complaints and making a decision which may range from a verbal or written reprimand to dismissal and legal action.
Taking this procedure into account, during 2018:
- Six cases of corruption were confirmed: 2 related to breach of confidence by accepting gifts or gratuities, 1 for conflict of interest by being related to the client, 1 for product theft, 1 for improper use of fuel card resources and 1 for improper authorization of finished product without charge to the customer.
- In addition, 13 employees were dismissed from the Company pursuant to complaints.
103-1. Management Approach
In Grupo Herdez we continue to work on strengthening a culture of legality with the workers, clients, suppliers and institutions with whom we work, reinforcing year after year the knowledge and diffusion of our Code of Ethics and grievance mechanisms. Through training sessions, communication campaigns and initiatives we strengthen the standards and values under which we operate, thus encouraging ethical behavior in our value chain.
Furthermore, we recognize the importance of having employees and strategic partners who share our integral approach to ethics, allowing us to have regulatory agents that reject and denounce illegal acts, such as corruption, bribery and any breach of human rights; key social issues which we are facing every day and which prevent us from having fair, peaceful and inclusive societies.
103-7. Management approach
Through the detection and management of new business opportunities, constant innovation, brand diversity, strategic distribution alliances and proper management of environmental and social resources, we have been able to overcome a constantly shifting market, uncertain economic scenarios and other challenges to achieve steady growth and cross borders. Furthermore, having a sustainability strategy aligned with the Sustainable Development Goals, together with our environmental and social efforts, we have positioned as one of the leading processed food companies, one of the major players in the ice cream segment in Mexico, and among the leaders of the Mexican food segment in the United States, as well as being present in 21 countries around the world.
406-1. Incidents of discrimination and corrective actions taken
In 2018, we gave the workshop "Promoting a culture of legality in the workplace" as part of the business strategy to reinforce our Culture of Ethics and strengthen the Culture of Legality issues. Any form of harassment or discrimination due to ethnic origin, religion, nationality, gender, sexual preference, marital status, age, disability or for any other reason is prohibited across all our working activities. Our Code of Ethics and other Policies can be found at: https://grupoherdez.com.mx/sustentabilidad/codigos-y-politicas/
During 2018, there were no cases of discrimination and/or harassment.
401-3. Parental leave
During 2018, 133 employees were given parental leave; 100 women and 33 men. Of these employees, 112 have returned to work after their leave and continue to work in the company 12 months later.
103-12. Management Approach
One of Grupo Herdez' priorities is to provide a working environment where our employees can develop their personal and professional abilities to the full. It is, therefore, highly important to attract, develop and retain the best talent, through training plans, ongoing development and feedback, merit awards, respect for collective bargaining and a culture of ethical performance.
102-56. External assurance
For the fifth consecutive year, our sustainability information has been audited by Ernst & Young México (EY). (Añadir link a carta de verificación)
102-54. Claims of reporting in accordance with the GRI Standards
The sustainability information has been compiled in accordance with the Global Reporting Initiative (GRI) Standards, Core option, the Sustainable IPC of the Mexican Stock Exchange, the principles of the United Nations Global Compact and the United Nations Sustainable Development Goals.
It should be mentioned that the report covers all the Group's strategic areas and that the information contained therein was obtained through the social responsibility committees, key areas and senior management, who provided consolidated data for each indicator.
102-53. Contact point for questions regarding the report
Corporate Offices
Monte Pelvoux 215, Col. Lomas de Chapultepec, Del. Miguel Hidalgo, C.P. 11000.Mexico City.
Telephone: +52(55) 5201-5655
Contact: Grecia Domínguez Leyva
102-52. Reporting cycle
Year after year, our integrated sustainability report presents the results, programs and actions in the areas of finance, social and environment that took place during the period.
102-51. Date of most recent report
The most recent previous report covered the most important events from January 1, 2017 to December 31, 2017.
102-50. Reporting period
The scope of the information in this report is from January 1, 2018 to December 31, 2018.102-49. Changes in reporting
This year, due to the traceability of information we are not reporting the total volumes of our packaging materials.
This year, we are incorporating agricultural supply information into the supply chain information, as total volume of raw materials acquired throughout the year and the total number of suppliers.
In the environmental topic, this year's report includes consolidated information from previous years to enable the reader to identify and understand the performance in 2018 compared to previous years.
We updated the Health and Safety at Work indicators and Water indicators in accordance with the GRI 2018 update.
102-48. Restatements of information
There were no restatements of information.
102-46. Defining report content and topic Boundaries
In 2016, using GRI methodology and by involving our main stakeholders—suppliers, employees and customers—in interviews, focus groups and scoring on a scale of 1 to 5, we updated our materials study to identify the topics with greatest impact by and on the company.
In 2018, we continued to work on the priority topics detected during 2016: ethics and anti-trust, risk management, supply chain management, environmental management and operating efficiency, customer health, legal compliance, business development, economic performance, innovation, product labeling, occupational health and safety, commitment and working conditions, and community engagement.
Also, during 2018, we held dialog sessions with the employees responsible for following up on each material topic to establish the management approach (DMA) for each one. These meetings addressed the how, why and what we are doing to mitigate the negative and enhance the positive impacts.
The results of the meetings can be found in the management approaches of each section within the GRI content index.
102-7. Scale of the organization
The Group's infrastructure comprises:
15 plants (13 in Mexico, one in the United States and one in Peru)
24 distribution centers (22 in Mexico and 2 in the United States)
7 tuna vessels
479 Nutrisa stores
9,762 employees
20,971 mp in Net Sales
3,517 mp EBITDA
2.2% of Net Profits in Social Investment
* mp: Million pesos
The Company was founded in 1914 and has been listed on the Mexican Stock Exchange since 1991 under the symbol HERDEZ * and on the OTC under the symbol GUZBY (Level 1 ADR).
102-6. Markets served
We are present in 21 countries in 6 different regions around the world:
North America
- Mexico
- United States
- Canada
Central America
- Guatemala
- El Salvador
- Honduras
- Nicaragua
- Costa Rica
- Ecuador
Caribbean
- Cuba
- Dominican Republic
- Jamaica
- Aruba
Europe
- Spain
- Germany
- Portugal
- Switzerland
- Czech Republic
- Russia
Oceania
- New Zealand
Asia
- South Korea
102-5. Ownership and legal form
We are a mercantile company which has traded on the Mexican Stock Exchange since 1991 under the symbol HERDEZ*, and since 1997 on the OTC market under the symbol GUZBY. We are also one of 30 companies that form part of the Sustainable Price and Quotations Index, which recognizes those companies with the best social, environmental and corporate governance practices.
102-4. Location of operations
We are present in 21 countries in 6 different regions around the world:
North America
- Mexico
- United States
- Canada
Central America
- Guatemala
- El Salvador
- Honduras
- Nicaragua
- Costa Rica
- Ecuador
Caribbean
- Cuba
- Dominican Republic
- Jamaica
- Aruba
Europe
- Spain
- Germany
- Portugal
- Switzerland
- Czech Republic
- Russia
Oceania
- New Zealand
Asia
- South Korea
102-3. Location of headquarters
Our corporate offices are at Monte Pelvoux 215, Lomas de Chapultepec, Ciudad de México, C.P. 11000.
102-2. Activities, brands, products, and services
We are leaders in the processed food sector and one of the main players in the ice cream category in Mexico, and among the leaders in the Mexican food segment in the United States.
We participate in a wide range of categories, including organic foods, tuna, burritos, ketchup, spices, guacamole, ice cream, mayonnaise, jam, honey, mole sauce, mustard, pasta, tomato puree, home-style salsas, tea and canned vegetables.
We sell our products through a portfolio of exceptional brands, which include Aires de Campo®, Barilla®, Búfalo®, Chi-Chi’s®, Del Fuerte®, Don Miguel®, Doña María®, Embasa®, Helados Nestlé®, Herdez®, La Victoria®, McCormick®, Nutrisa®, Wholly Guacamole® and Yemina®.
In addition, we have product distribution agreements in Mexico with Frank's®, French's®, Kikkoman®, Ocean Spray® and Reynolds®.
102-14. Statement from senior decision-maker
Message from the Chief Executive Officer and Chairman of the Board Read more
102-13. Membership of associations
Industry
- Mexican Association of the Coffee Production Chain (Asociación Mexicana de la Cadena Productiva del Café, AMECAFE)
- National Chamber of Metal Can Manufacturers (Cámara Nacional de Fabricantes de Envases Metálicos, CANAFEM)
- National Chamber of the Food Preserves Industry (Cámara Nacional de la Industria de Conservas Alimenticias, CANAINCA)
- Mexican Council of the Consumer Products Industry
- Mexican Council of the Consumer Products Industry (CONMEXICO)
- National Agricultural Council (Consejo Nacional Agropecuario, CNA)
- National Council of Organic Production (Consejo Nacional de Producción Orgánica, presided over by SAGARPA)
- International Federation of Organic Agriculture Movements (IFOAM)
- Mexican Organic Movement (Movimiento Orgánico Mexicano)
Business
- Mexican Association of Electronic Business Standards (Asociación Mexicana de Estándares para el Comercio Electrónico, AMECE)
- Foreign chambers of commerce: Canadian, British, Spanish and American
- Confederation of Industrial Chambers (Confederación de Cámaras Industriales, CONCAMIN)
- Business Coordinating Council (Consejo Coordinador Empresarial, CCE)
Sustainability
- Mexican Center for Philanthropy (Centro Mexicano para la Filantropía)
- Private Sector Study Commission for Sustainable Development (Comisión de Estudios del Sector Privado para el Desarrollo Sustentable, CESPEDES)
- Business Commitment for the Integral Management of Solid Waste (Compromiso Empresarial para el Manejo Integral de Residuos Sólidos)
- Basin Councils (Consejos de Cueca, in CONAGUA)
- ECOCE, A.C.
- Iniciativa GEMI
- United Nations Global Compact
102-11. Precautionary Principle or approach
Grupo Herdez is currently engaged in an Organizational Life Cycle Assessment (LCA) to calculate the environmental footprint of its main product categories. The aim is to detect opportunities to reduce environmental impacts in the supply chain and create synergies with the external actors and Stakeholder groups that intervene in our chain of production. The results of the LCA will be used to develop an action plan--with short, medium and long-term horizons--prioritizing the projects with greatest impact and taking into account the following criteria: reducing the environmental footprint, profitability for the business and ease of implementation.
Grupo Herdez, aware of the environmental, safety and quality risks that may arise in the framework of its operations and to ensure that its impacts on society and the environment are positive, approaches the precautionary principle (environmental, safety and quality risks) in two stages
Internally, through the Environmental Control, Safety and Hygiene (CASH) area, whose aim is to safeguard the integrity of employees and facilities, support operating continuity through compliance with applicable regulations and collaborate in the protection of assets.
Each of our locations has a work program aligned with the goals of Grupo Herdez for CASH; the program is based on risk studies and backed by safety and hygiene regulations to measure risks pertaining to machinery, equipment, storage, chemical control, work environment, noise, and high and low temperatures.
Preventive Plans
We have a World Class Manufacturing (WCM) scheme, whose goal is continued improvement across all our plants. This program has helped us to:
- Achieve competitive costs.
- Improve productivity.
- Have a quality reference.
- Attain world class management and operation.
- Have effective information systems.
Similarly, we have a major emergency plan, designed to respond to any contingency in plants and distribution centers. The plan involves brigades which support and coordinate communication between affected, adjoining and corporate areas. Five contingencies arose in 2017.
Membership in Associations
We participated in Coparmex as a consultant and adviser on safety and hygiene and environmental matters, and were active members of the CONMEXICO safety committee.
Certifications
Environment
- Clean Industry Certification, issued by the Federal Environmental Protection Agency (PROFEPA). In 2018, we maintained our certification in 4 plants.
- Marine Stewardship Council Certification, which establishes the standards for sustainable fishing and traceability of sustainable fishing products.
Safety
- Safe Industry certification issued by the Secretariat of Labor and Social Welfare (STPS).
Quality
- Certification issued by the Federal Commission for Protection against Health Risks (COFEPRIS).
Civil Protection
- Every year, an internal protection program is run, audited by internal personnel and focused on the prevention of fire, spills, leaks and other risks.
102-10. Significant changes in the organization and its supply chain
In September 2018, a new Distribution Center was opened in Villahermosa, Tabasco, with a surface area of 6,000 square meters and the capacity for 6,000 pallets.
102-1. Name of the organization
Grupo Herdez, S.A.B. de C.V.
102-42. Identification and selection of stakeholders
Stakeholders are defined as those main internal and external actors with whom we have established a close win-win relationship that fosters the growth and sustainable development of both parties.
102-36. Process for determining remuneration of the highest governance body
The Corporate Practices Committee is responsible for validating the remuneration of the Company’s senior executives, including the Chief Executive Officer.
102-35. Remuneration policies for the highest governance body
In accordance with Company bylaws, the remuneration received by Board members is three 50-peso gold coins (centenary commemoration coins) or their equivalent for attending each meeting; this remuneration is not dependent on the Group’s profits.
102-31. Review of economic, environmental and social topics
The Board meets quarterly and has intermediate bodies in charge of overseeing the management and execution of the Company’s objectives. A sustainability performance report is presented during the board meetings, which covers environmental performance and quality of life indicators for employees.
102-29. Highest governance body’s role in identifying and managing economic, environmental and social topics and their impacts, risks and opportunities
The Board meets quarterly and has intermediate bodies in charge of overseeing the management and execution of the Company’s objectives. A sustainability performance report is presented during the board meetings, which covers environmental performance and quality of life indicators for employees.
102-26. Role of highest governance body in setting purpose, values and strategy
The Board meets quarterly and has intermediate bodies in charge of overseeing the management and execution of the Company’s objectives. A sustainability performance report is presented during the board meetings, which covers environmental performance and quality of life indicators for employees.
102-25. Conflicts of interest
Each Board member signs a declaration of absence of conflict of interest, and each Committee has regulations that establish its functions and relationship with the Board of Directors.
Furthermore, our Code of Ethics and Conflict of Interest Policy are binding documents and obligatory for all employees. They can be viewed at: https://grupoherdez.com.mx/sustentabilidad/codigos-y-politicas/102-24. Nominating and selecting the highest governance body and its committees
Board members are ratified by shareholder vote at the Annual Meeting. To be selected, Board members must meet the following requirements:
i) professional training in economic-administrative sciences, preferably with a master’s degree in those areas; ii) twenty years’ minimum professional experience in executive positions with consumer companies and/or the finance sector; iii) experience as a board member in manufacturing industry companies and/or the finance sector; and iv) belong to business organizations.102-23. Chair of the highest governance body of the organization
The Chairman of the Board, Héctor Hernández Pons Torres, is also the Chief Executive Officer.
102-21. Consulting stakeholders on economic, environmental and social topics
In 2016, using GRI methodology and by involving our main stakeholders—suppliers, employees and customers—in interviews, focus groups and scoring on a scale of 1 to 5, we updated our materials study to identify the topics with greatest impact by and on the company. In 2018, we continued to work on the priority topics detected during 2016: ethics and anti-trust, risk management, supply chain management, environmental management and operating efficiency, customer health, legal compliance, business development, economic performance, innovation, product labeling, occupational health and safety, commitment and working conditions, and community engagement.
102-20. Executive-level responsibility for economic, environmental and social topics
During the quarterly Board meetings, a sustainability performance report is presented, which includes environmental performance and quality of life indicators for collaborators. The board members responsible for the report are:
Labor Practices: José Manuel Rincón Gallardo
Environmental Practices/Climate Change: Luis Rebollar Corona
Corporate Governance: José Roberto Danel DíazAll Board members are over 50 years and 78% are men.Furthermore, in 2016, Grupo Herdez set up an Energy Committee, which is comprised of directors from the different areas of the Company, including the Chairman of the Board. The committee is responsible for defining the strategic goals in terms of energy, such as: energy procurement, cogeneration, efficiency projects, etc., and meets twice a year.
102-19. Delegation of authority
During the quarterly Board meetings, a sustainability performance report is presented, which includes environmental performance and quality of life indicators for collaborators. The board members responsible for the report are:
Labor Practices: José Manuel Rincón GallardoEnvironmental Practices: Luis Rebollar CoronaCorporate Governance: José Roberto Danel Díaz.
Ninety percent of board members are over 50 years and 78% are men.
102-17. Mechanisms for advice and concerns about ethics
All levels of authority within the company and stakeholder groups, including suppliers and employees, are governed by our codes and policies (http://grupoherdez.com.mx/sustentabilidad/codigos-y-politicas/), which are constantly reinforced through training sessions, communications and meetings.
To prevent any kind of unethical behavior or situation which undermines the integrity of our employees and/or suppliers, and consequently the company, we have grievance mechanisms that are monitored by an external supplier, and assessed by the internal audit team and the Human Resources Department.
Our internal stakeholders can file complaints through:
- E-mail: [email protected], [email protected]
- E-mail and direct line to the supervisors of Human Resources, Internal Audit and Legal.
- Physical mailboxes inside different locations
- Toll-free line 01 800 CONFIANZA (01 800 266 342 692) or (Nutrisa 01800 312 98 32)
These mechanisms are available 365 days a year, 24 hours a day.
The most used mechanism is the 01 800 confianza line which received more than 60 percent of the grievances or complaints filed; during 2018, 22 grievances and 81 complaints were received, of which 93 percent have been resolved, the remaining 7 complaints were made in the 4th quarter of 2018 and are in the process of being dealt with.
102-16. Values, principles, standards and norms of the organization
Mission
To place quality foods, beverages and products within the reach of consumers, under brands of growing prestige and value.
Vision
Grupo Herdez aims to consolidate, grow and position itself as a leading company in the food, beverage and wellness products industry, recognized by the quality of its products and the effectiveness of its efforts in satisfying the clients' and consumers' needs and expectations, within a framework of optimal consumer care and service, under strict profitability criteria, strategic potential and sustainability.
Values
Honesty, Achievement Focus, Team Work and Trust.
IP-2. Percentage of operations with implemented community engagement, impact assessments and development programs
Community Engagement Chapter Read more
103-10. Management approach
Grupo Herdez is committed to the social and environmental needs of the places where we operate, and we strive to make our programs and projects increasingly aligned with a vision of sustainability. That is why we are perfecting our strategy and we present the alignment of our four action pillars with 7 Sustainable Development Goals, in order to make a positive contribution to the 2030 Agenda proposed by the United Nations. One of our main commitments, and the most important to us, is Zero Hunger.
In addition to the above, due to our business activity as a leading company in the food, beverage and wellness product sector, we focus our sustainability and social responsibility efforts on contributing to food security in Mexico. Therefore, we improve the bioavailability of nutrients, contributing to healthy and affordable nutrition, and mitigating food waste through two central programs: generating and installing productive projects in rural communities through the Saber Nutrir program, in partnership with associations such as ChildFund and Pro Mazahua. We also make a monthly food donation to the Mexican Food Bank, an association that provides food to populations living with food poverty across the nation.
All of our community outreach and support programs are intended to improve the quality of life and nutritional condition of their beneficiaries.
IP-1. Customer and client relations
To address the comments and needs of our customers and consumers, we have various means of communication.
Points of contact
01-800 Lines: each brand has an assigned number for resolving problems with quality, complaints, or product suggestions. This year we received a total of 737 calls and 947 e-mails. Each one generates a follow-up report, and in case of product complaints, we also track their status and/or resolution process.
Digital methods: we have official websites for most of our brands, where consumers and customers may find all of the related information. We also have more than 20 profiles on brand social networks, where the interaction of “Q & A” allows us to monitor our successes, concerns and questions from our customers.
www. | YouTube | Other | ||||
Grupo Herdez | X |
| X | X |
|
|
Aires del Campo | X | X | X |
| X | 1 |
Barilla | X | X | X | X |
|
|
Blasón | X | X |
|
| X |
|
Búfalo | X | X | X | X | X |
|
Carlota | X |
|
|
|
|
|
Chi-Chi's | X | X |
|
| X |
|
Del Fuerte | X | X |
| X |
|
|
Don Miguel | X | X |
|
|
|
|
Doña María | X | X |
|
|
|
|
Herdez | X | X |
|
|
| 1 |
McCormick | X | X |
| X |
|
|
Helados Nestlé |
| X |
|
| X | 2 |
Herdez Brand | X | X |
|
|
| 1 |
Nutrisa | X | X | X |
| X |
|
Vesta |
|
|
|
|
|
|
La Victoria | X | X | X | X | X | 2 |
Wholly Guacamole | X | X | X | X | X | 2 |
Yemina | X |
|
|
|
|
|
Distribution Agreements | ||||||
Kikkoman México | X | X |
| X |
|
|
Ocean Spray | X | X |
|
|
|
|
Reynolds | X | X |
| X |
|
|
IP-8. Policies and practices for notifying consumers about ingredients and nutritional information in addition to legal requirements
Labeling Requirements
Regulatory labeling requirements that are relevant to the product market vary, depending on the product category. The specific Official Mexican Standard (NOM) applies to the domestic market. If none exist, general guidelines and regulations apply, such as: Sanitary Control for Products and Services; the General Health Law on Sanitary Control of Activities, Establishments, Products and Services; Agreement for Determining the Additives and Processing Aids in Food, Beverages and Food Supplements, their Use and Sanitary Arrangements; Arrangement to Determine Prohibited or Permitted Plants for Teas, Infusions, and Edible Vegetable Oils, among others.
For export products, we apply the applicable regulation from the country to which they will be exported.
As a voluntary practice that goes beyond legal requirements, we reviewed the sub-ingredients of the raw materials included in the formula to manifest any additive or pollutant that could affect product safety. In addition, we requested results from a pollutant analysis from certain suppliers, depending on the nature of the ingredient or product, especially for those products exported to the United States.
Information on Contents and Ingredients
All of our products in the Food, Non-Alcoholic Beverage and Food Supplement categories include a corresponding list of ingredients and nutritional information.
- For Food and Beverages, it is mandatory to include energy content, proteins, total fat, saturated fat, carbohydrates, total sugars, dietary fiber, and sodium.
- For Supplements, we must include energy content, protein, total fat, carbohydrates and sodium per portion and per 100 g.
The main source of nutritional information is the label. However, some of the Company web pages include that information. In addition, the 01800-customer service line for each of the food and non-alcoholic beverage brands has the corresponding and up-to-date information.
All statements made on the labels must be supported by scientific evidence in order to include them on the lable and in compliance with the regulation that applies to that product and to the market where the product will be sold.
Within these internal guidelines, we have agreed to include the following on the label:
- Whether the coloring is artificial or natural
- If the flavor is natural, artificial, or identical to natural
- Hydrolyzed protein and MSG are declared as is
- There is no statement policy for GMO, in accordance with national legislation
- Sweetening agents are declared, as required by the Additive Agreement
- All present allergens and those that could be present in the product are declared
- Practically none of our products are fortified, unless required by law
- The methods used to process the foods to maintain their safety are listed
417-2. Incidents of non-compliance concerning product or service information and labeling
In 2018, there were 4 incidents related to our product labeling, 3 of which resulted in a monetary fine and one which produced a verbal warning.
HERDEZ CEDIS EL DUQUE: McCormick infusions were immobilized. Product was released for reconditioning.
McCORMICK EL DUQUE PLANT: McCormick infusions were immobilized.
NUTRISA: Product was halted at the branch in Las Américas, Xalapa, and at the branch in San Esteban, Naucalpan, due to finding product at no charge. Product was halted at the Galerías Atizapán branch in the State of Mexico, because of expired product.
416-1. Assessment of the health and safety impacts of products or services
The Research & Development Departments at Grupo Herdez, Helados Nestlé and Nutrisa are responsible, not only for conceptualizing products that anticipate or adapt to changing lifestyles and the needs of our customers and consumers, but also make required modifications in terms of health, safety, quality and nutrition for our broad portfolio of existing products.
Herdez
In 2018, the range of canned vegetables was reformulated with a reduction in sugars and we began to work on reformulating certain products that will be launched in 2019, with the goal of making them healthier.
The reduction of added sugars was applied to different presentations:
- Corn kernels
- Bean salad
- Vegetable salad
- Peas and carrots
- Baby peas
Nestlé
Of our products, 4% were evaluated and improvements were formulated to impact health.
We developed 10 transformation projects in 7 SKUs of the 159 that were marketed in 2018.
- Switched to natural flavors - Nesquik frozen pop, Lápiz de Color, Galactea and Pelapop
- Reduced sugar - Galactea frozen pop, Pelapop, Nieve Lápiz de Color, Carlos V ice cream.
- Reduced calories - Carlos V frozen pop
- Reduced saturated fats - Galactea frozen pop
All of the products that were marketed and manufactured under the Nestlé brand are evaluated under Nutritional Foundation criteria, which define very strict parameters for caloric content (kcal), added sugar (g/portion), total fat (g/portion), saturated fat (g/portion) sodium (mg/portion) and fructose (g/portion). Compliance with these criteria is mandatory for any product intended for children.
IP-5. Types and rates of injuries, occupational diseases, lost days, absenteeism, and work-related fatalities
Since 2012, the Environmental Control, Health and Safety (CASH) Department operates under a strategic plan to follow-up incidents and prevent workplace accidents and environmental damage.
Thanks to this ongoing effort, in 2018, we reduced our Accident Rate by 19% and reduced the Lost Work Days Rate by 22%.
Year | Gender | Accidents | Accident Rate * | Days lost due to accidents | Days lost due to accident rate |
2018 | Women | 81 | 1.55 | 934 | 17.83 |
Men | 98 | 1.41 | 1,843 | 26.54 | |
Total | 179 | 1.47 | 2,777 | 22.79 |
Year | Gender | Accidents | Accident Rate * | Days lost due to accidents | Days lost due to accident rate** |
2017 | Women | 68 | 1.5 | 1,024 | 22.52 |
Men | 147 | 2 | 2,423 | 33.02 | |
Total | 215 | 1.81 | 3,447 | 29 |
(*) The accident rate expresses the number of accidents during the year in relation to the total man-hours worked multiplied by a factor of 200,000.
(**) The days lost rate expresses the total number of days lost during the year in relation to the total man-hours worked multiplied by a factor of 200,000.
The information shown here covers all Group employees, since the Company does not have subcontracted personnel.
403-8. Health and safety management system
The Environmental Control, Health and Safety Department (CASH) monitors our health and safety management systems. These systems apply to all of the Grupo Herdez facilities, including Plants, CEDIS, Stores and Corporate Offices. Likewise, they cover all personnel working or within any of our facilities.
The Occupational Health and Safety systems are in effect for employees and workers who are not employed by Grupo Herdez.
This training includes all Grupo Herdez personnal as well as workers who are not employed by the company but whose work and/or place of work is controlled by the organization.
Number of Workers | Total Percentage Covered by the SG (%) | Percentage Internally Audited the SG (%) | Percentage Audited/Certified by Third Parties (%) | Observations |
1,527 | 100% | 2-3% | 0% | At all Grupo Herdez facilities, all personnel, whether internal or external, is trained in order to work. All are governed by the Grupo Herdez systems, rules and safety procedures. |
403-7. Prevention and mitigation impacts
Grupo Herdez has an Industrial Safety Policy that applys to any person working or within the Group’s facilities, as well as contracted or subcontracted personnel. The Industrial Safety Policy may be viewed at https://grupoherdez.com.mx/conocenos/codigos-y-politicas/
403-6. Promotion of worker health
Grupo Herdez facilitates worker access to medical and health services. We have the following mechanisms:
Strategy | Scope | Evidence |
File composition | Worker conformity assessment | Staff medical exam |
Medical consultation at Plants | For all workers | Medical consultations and their records |
Integration into internal health campaigns | For all workers, where applicable | Attendance or assessment lists |
Work risk exam | When required to perform a job deemed to be risky | Medical assessment and/or work permit |
Private Institutions | For all workers | Service contracts or purchase orders |
Regulatory Health Studies | Audiometry |
|
In addition, we offer voluntary services and health promotion programs that are not related to work.
Service / Program | Description | Evidence |
Medical guidance in case of illness | The employee must notify his or her immediate supervisor of any anomaly or discomfort to be sent and attended to in the Plant’s medical office, to receive assessment and medical guidance. | Medical leave, care log |
Prevenimss | Prevenimss campaigns to apply vaccines, measure stature, weight, blood pressure, etc. |
|
Seasonal Illnesses | Newsletters to prevent seasonal illnesses in summer, autumn and winter |
|
Get rid of standing water | Campaign to prevent the proliferation of vector-borne diseases such as dengue, zika, among others. |
|
ISEMIM health campaigns | Campaigns for de-worming, breast cancer, prostate cancer, etc. | Photographs, records |
Government hospitals | Prevention campaigns, conferences | Attendance lists, records |
Annual health campaigns | Prevention campaigns for staff on health topics, taught by external personnel, and a visual health campaign |
|
Internal nutrition campaign for personnel in situations involving excess weight and nutritional control | For all workers |
|
Prevenimss campaigns to apply vaccines, measure stature, weight, blood pressure, etc. | For all workers |
|
All employee medical information is strictly confidential. To ensure this is maintained, we apply our Code of Ethics.
If any illegal or unethical situation is detected, all of our stakeholders may report non-compliance through:
- E-mail: [email protected], [email protected]
- E-mail and direct line to the supervisors in the Human Resources, Internal Audit and Legal Departments
- Physical mailboxes in different locations
- Phone line 01 800 CONFIANZA (1 800 266 342 692) or (Nutrisa 01800 312 98 32)
These mechanisms are available 24 hours a day, 365 days a year.
403-5. Training on occupational health and safety
Occupational health and safety training are a main CASH activity.
This training includes all Grupo Herdez personnal as well as workers who are not employed by the company but whose work and/or place of work is controlled by the organization.
Training | Description / List of Topics |
Safety Training | Identification of unsafe actions and conditions, policies, regulations and safety management systems |
STPS Standards | Annual training in applicable standards from the STPS, at the knowledge level for all operational personnel and at the mastery level for specialized personnel, according to the work site, including AR and AST. |
SafeStart | Safety philosophy that promotes a culture of safety by raising awareness among the personnel, producing safety habits that reduce the occurrence of injuries caused by human behavior status, critical errors, and practicing error reduction techniques (5 modules). |
Lock Out / Tag Out (LOTO) | Technical training for lock out systems for essential operating, maintenance and cleaning jobs where personnel are required to intervene in moving equipment and/or that uses electrical power, in order to eliminate dangerous energy sources that could put workers in danger. |
Emergency Response | Training personnel in response activitties for emergencies related to operations such as: natural disasters, firefighting, first aid, evacuations, search, rescue, spill response, sabotage, etc. |
CT PAT | Employer safety (facility safety, personnel safety, training, transportation, reporting culture, information systems, process and internal) |
STOP | Safety process to identify and correct unsafe actions in the workplace |
403-4. Worker participation and consultation
Grupo Herdez has various processes to foster worker participation and consultation in the development, implementation and assessment of the management system. Likewise, they also provide access and to communicate relevant information on occupational health and safety topics to our workers. They are:
Process | Description |
5 S System | This complies with the 5 S system through visible standards and regulations in each area for easy comprehension and identification by all personnel, giving them the power to deny entry to any person who does not comply with the requirements in the standards. |
CASH Notice Boards | Develop the dissemination of information about campaigns, invitations to participate in workplace health and safety activities, and accident rate indicators. |
Comprehensive Management System | Safety patrols and/or audits are scheduled to assess compliance. When needed, action plans are established based on the hazards that are identified. Likewise, feedback is provided for the areas involved for ongoing improvement with good safety performance. |
Notices, newsletters, pamphlets, and visual aids | Production of informative notices with relevant information and scheduled events for topics oh safety, health, and/or the environment |
Health Programs | Based on the contents of the annual health program, different occupational health campaigns are carried out, including vaccination, early detection of chronic-degenerative diseases, studies on occupationally exposed personnel, analysis of febrile reactions and follow-up with medication. |
Mailboxes | Comments and observations may be sent through cards deposited in the physical mailboxes at each location. These mechanisms are available 24 hours a day, 365 days a year. |
We have health and safety management committees to provide timely follow-up for each relevant topic, described as follows:
Committee | Responsibility | Meeting Frequency | Degree of Authority |
Health and Safety Commission | Strategic patrols to identify unsafe acts and/or conditions | Monthly | Medium |
CASH Pillar | Execute and implement safety methodology, participating in the analysis of accidents, actions, and early attention to unsafe conditions. | Weekly | High |
Strategic Plant Committee | Important decision-making on strategic points | Monthly | High |
Environmental Control, Health and Safety (CASH) | Management duties on occupational health and safety | Weekly | High |
In addition, we have formal local agreements with the unions, to benefit the workers, on occupational health and safety such as: emergency brigades, evacuation and firefighting brigades, workplace disease and accidents, health and safety campaigns, workplace risk prevention system, and all those mandated by law, regulation, and the Official Mexican Standards.
403-3. Occupational health services
The definition of participation in Occupational Health (Medical Service) begins in a safety patrol program, which highlights unsafe conditions. Based on the Risk, an annual program is established with general and special tests such as spirometry, audiometry, vibrations, lower and/or elevated thermal conditions, etc.
Medical files are kept strictly confidential and solely for physician-patient knowledge.
403-2. Hazard and risk identification
Identification
The main process for identifying occupational hazards and risk evaluation is through the Comprehensive Environmental Control, Health and Safety Management System (SAI CASH).
This internal system is based on adherence to regulatory monitoring, including preventive observation of conduct. That is why we provide training on the 5 Ss in Job Safety Analysis (JSA).
Monitoring
To ensure proper compliance with SAI CASH, we prepare measurements and indicators that are strategically reviewed on a weekly, monthly and annual basis. From the monthly and annual results, we prepare work plans for the subsequent year, which are approved by local management, CASH management and the Office of the Supply Chain.
Ongoing improvement
The results of the CASH measurements and indicators highlight areas of opportunity, which are established in future work plans. In addition, weekly meetings are held with safety leaders, who present the progress made in timely follow-up for each area of opportunity that was identified.
Reporting Identified Hazards
The main reporting process is through cards left in mailboxes, reports that are documented through verification lists, and through reports by the Health and Safety Commission.
The three reports mentioned above are confidential. A Review Committee is involved in the reporting process, aided by management, which provides specific, case-by-case support.
Policies and Processes in Case of Incidents
Policy / Process | Description |
Preventive Observation System | The hazardous situation is identified and is reported according to its relevance and importance, based on the impact that it could have. Once it has been analyzed, a determination is made as to whether the process requires an operational shutdown until the situation is resolved. |
Industrial Safety Policy | Supported by the commitment of the Head Office Includes topics on safety, health, environment |
5 S System | Standards are visible in each department, along with regulations with the entry standards. If there is a compliance failure at any time, any person may decide to deny into any area backed by the implementation of these programs. |
Accident Investigation /Health and Safety Commission | Once any type of accident is detected, area supervisors or managers are gathered with the Health and Safety Commission to determine its root cause. Once the situation has been reviewed, a news flash is published that specifies the situation, causes, and actions taken. |
403-1. Health and safety management system
The Environmental Control, Health and Safety System (CASH) monitors our health and safety management systems. These systems apply to all of the Grupo Herdez facilities, including Plants, CEDIS, Stores and Corporate Offices. Likewise, they cover all personnel working or within any of our facilities.
The Occupational Health and Safety systems that are implemented for employees and workers who are not employed by Grupo Herdez but whose work and/or place of work is controled by the organization are:
Systems | Standares / Guidelines Used as Basis | List of Standards / Guidelines |
SAI CASH | STPS Standards | NOM-001-STPS-2008, NOM-002-STPS-2010, NOM-004-STPS-1999NOM-005-STPS-1998, NOM-006-STPS-2014NOM-009-STPS-2011, NOM-010-STPS-2014NOM-011-STPS-2001, NOM-015-STPS-2001NOM-017-STPS-2008, NOM-018-STPS-2015NOM-019-STPS-2011, NOM-020-STPS-2011NOM-022-STPS-2015, NOM-024-STPS-2001NOM-025-STPS-2008, NOM-026-STPS-2008NOM-027-STPS-2008, NOM-028-STPS-2012NOM-029-STPS-2011, NOM-030-STPS-2009NOM-033-STPS-2015, NOM-034-STPS-2016 |
WCM (World Classs Manufacturing) | Official Mexican Standards, Industry Best Practices | |
SafeStart | SafeStart | Safety based on behavior |
Work System Based on Direct Observation | STOP | Detection and correction of unsafe actions |
Employer Safety System | CT PAT | Facility Safety, Employee Safety, Personnel Training |
OHSAS 18001 | International standard focused on occupational health and safety topics | List of Official Mexican Standards that are applicable to the business activity as well as international standards focused on occupational health and safety topics |
The above has allowed us to safeguard the integrity and well-being of our operational personnel, prevent and mitigate incidents that could affect the environment, and maintain a culture of safety and risk prevention, thereby guaranteeing the continuity of our operations.
IP-9. Developing a Healthcare and Nutrition Strategy
Within the Technical Division, the Scientific and Regulatory Affairs Department ensures that the products developed by Grupo Herdez contain permissible ingredients in the doses indicated by the Regulations that are applicable to each product category. It also determines which nutritional icons must be placed on each front label, so that customers have the nutritional information for each product.
Likewise, the Technical Division ensures that new and existing products comply with the regulatory framework that is applicable to each product category, ensuring their quality and safety, and in compliance with national and international standards in terms of health and nutrition.
In the innovation, development and reformulation of already-existing products, the recommendations issued by the World Health Organization are taken as a reference in terms of nutrition and healthy eating, for international standards.
At the national level, references are taken from the NOM-086-SSA1 (Non-Alcoholic Drinks and Foods with Modifications to their Composition) and NOM-051-SCFI/SSA (General Labeling Specifications for Pre-Packaged Non-Alcoholic Drinks and Foods).
In 2018, the range of canned vegetables was reformulated with a reduction in sugars and we began to work on reformulating certain products that will be launched in 2019, with the goal of making them healthier.
IP-7. Innovation Management
Innovations for processes are under consideration for future years and will include more sustainable packaging technology.
Expenses in I&D over the past two years has been as follows:
| Unit | 2017 | 2018 | |
Total R&D Expenses | Millions of pesos (MXN) | $13,115,879.21 | $18,112,998.00 | |
Number of R&D positions | FTEs* | 33 | 43 | |
R&D spending as% of sales | Spending MXN / % of net sales from innovation | 5.9% | 7.2% | |
FTEs* full-time employees |
|
|
Grupo Herdez seeks to promote open innovation in order to contribute to external knowledge and to supplement our internal I&D strategy. In 2018, our most successful project was Show Off Your Salsa.
Project | Description | Quantitative Impact on R&D Cost/Benefit | Benefit | |
Show Off Your Salsa | Through a promotion, we asked customers to send us their recipes so that the winners could be launched as part of our portfolio of salsas. The recipes were produced by our customers and we received more than 12,000 recipes. | In 2018, we generated 4.2 MDP of sales in 3 months | We produced a positive customer reaction by actively involving them in an innovative process. We have a pipeline of 12,000 recipes for the subsequent years. Increase in household penetration | |
In 2018, the income generated by product innovations, new products and products with significant improvements were:
Percentage of income (in %) | 1.75% |
New products or services marketed during the past year (2018) | 23 |
Products with significant improvements tha were marketed during the past year (2018) | 8 |
Products or services without changes or minimal modifications | Rest of the portfolio |
Total | 100% |
201-2. Financial implications and other risks and opportunities due to climate change
Since we are a leader in the food industry, we have a high dependence on natural resources, especially agricultural supplies and water. Therefore, in order to guarantee the continuity of our operations and continuous growth, it is essential to anticipate and manage the impacts produced by environmental changes.
Therefore, in addition to our environmental actions to reduce our atmospheric emissions and take care of biodiversity, such as reducing fuel consumption and the use of electrical power, we have the Renewable Energy Cogeneration Project, the use of wind energy and the Agricultural Sustainability Plan.
In 2018, we are perfecting our strategy and we present the alignment of our four action pillars with 7 Sustainable Development Goals. They allow us to highlight our environmental priorities: Clean water and sanitation, Responsible Consumption and Production, Climate Action and Life Below Water.

In addition, we continue to work on projects that are highly challenging, but that have great impact on our business strategy: Organizational Life Cycle Assessment and Climate Change Risk Study. Both projects will allow us to identify the key activities with the most impact, the associated business risks, opportunities for efficiency, and to implement corporate planning actions for environmental sustainability.
Both projects will wrap up in 2019.
Organizational Life Cycle Assessment
This tool is used to quantify the environmental impact of a product, service or organization by taking all of the stages in the supply chain into consideration.
This analysis will allow us to identify our main environmental impacts caused by our main products and the areas of opportunity to reduce our ecological footprint, in its various expressions (water footprint, carbon footprint, among others).
Advances
- Plant and CEDIS visits
- Selection of categories and SKUs
- Workshops with agricultural suppliers: identifying available information on the impact, probability and resilience to climate change risks and information requirements.
Universe: Approximately 81% of total production and 49% of SKUs.
Climate Change Risk Study
The purpose of the Climate Change Risk Study is to identify the impact of climate change on the Group’s business continuity. We will use it to prioritize the business risks and perform an assessment of the financial impact to be able to propose manageable initiatives.
Advances
- Identification of risks through a risks and resilience questionnaire given to agricultural suppliers
- Collection of important information - internal and external - on the topic
- Identification of the most relevant risks at the point on the value chain where they could materialize, taking into consideration the probability of occurrence and the impact that could be produced
The identified risks have been classified based on their probability of occurrence and impact, so it is possible to prioritize those deemed most relevant and to inform the decision-making process to manage them in the most appropriate manner, regardless of whether or not they materialize in our own operations, in the supply chain, or in our relationships with our stakeholders.
According to the considerations listed above, the following map presents the main climate change risk factors that have been identified: Increase in temperature and its impact on the supply chain, changes in precipitation patterns and changes in consumption habits.The study is expected to conclude in 2019 and an action plan will be defined in order to manage the identified risks.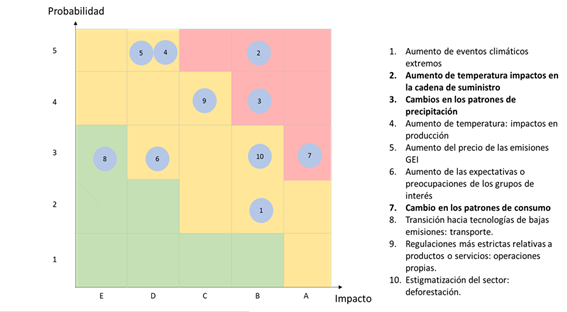
IP-6. Agricultural Sustainability Plan
The purpose of the Agricultural Sustainability Program is to generate high quality food products, avoid altering the balance in the environment, use natural resources appropriately and maintain their integrity for future generations.
The main benefits of the Program include reducing costs for our suppliers, reducing environmental impact and producing agricultural raw materials with fewer chemical residues, thus achieving higher quality.
Through the Good Practices Manual, training sessions and environmental audits, we support our agricultural suppliers in their adoption of best labor and environmental practices. In 2018, we held two training sessions on:
- Integrated Crop Management
- Agricultural Sustainability
Audits
In order to provide continuity and validity to our progress in the Agricultural Sustainability Plan, we have a team of six internal auditors who evaluate and monitor the status of the properties. They monitor whether the suppliers are located in environmentally sensitive areas and the measures that are being implemented to protect them, as well as the measures adopted to improve soil quality, increase recycling and reduce waste production. They do this using a checklist that measures progress and improvement points for each supplier.
Our auditors have the Produce Safety Alliance certification.
The producers are audited based on the guidelines contained in the Good Hygiene Practices Manual for Agricultural Products, with two main criteria: Good Agricultural Practices Manual and Agricultural Sustainability Program.
In 2018, 38 suppliers were evaluated against the Good Agricultural Practices criteria and 37 against the Agricultural Sustainability Program criteria.
The main existing controls to monitor advances in the implementation of the Plan are:
- Delivery of documentary control at the beginning of the contract. Frequency: yearly
- Periodic monitoring of each supplier. Frequency: biweekly
- BPA Auditors. Frequency: quarterly
- Water, soil and fruit analysis. Frequency: only once for water and soil; fruit is monthly.
Agrichemical Use
The main objective in reducing the use of agrichemicals falls under the Integrated Crop Management (use of biological products).
Type | % Reduction | |
| 2017 | 2018 |
Pesticide | 10% | 16% |
Of all of our agricultural suppliers, the percentage of compliance with the Good Agrochemical Handling and Useage is:
2017 | 2018 |
60% | 90% |
301-1. Materials used by weight and volume
In 2018, the total of renewable materials, including agricultural raw materials, was:
Renewable Materials (ton) | 2017 | 2018 |
Raw Materials | ||
Corn Oil | 80 | 102 |
Palm Oil | 34 | 45 |
Soy Oil | 104,136 | 109,110 |
Kernel Oil | 847 | 1,002 |
Oils, Fats and Derivatives | 33 | 76 |
Sliced Olives | 2 | 4 |
Acids | 665 | 758 |
Dehydrated Garlic | 261 | 207 |
Alcohol | 646 | 673 |
Almonds | 48 | 59 |
Starches | 3,164 | 2,944 |
Water resin | 1 | 1 |
Sugar | 8,295 | 8,750 |
Cacao | 61 | 72 |
Dehydrated Meat | 28 | 34 |
Dehydrated Onion | 262 | 319 |
Cereals and Fibers | 108 | 128 |
Mushroom Chunks and Slices | 15 | 2 |
Dehydrated Peas | 2,174 | 1,304 |
Dehydrated Hot Peppers | 49 | 57 |
Chocolates | 92 | 112 |
Coatings | 1,113 | 1,080 |
Cocoa | 125 | 131 |
Ice Cream Colors | 107 | 62 |
Dry Colors |
| 82 |
Lemon Juice Concentrate | 384 | 396 |
Fruit Concentrates | 59 | 106 |
Cream for Ice Cream | 109 | - |
Sweetening agents | 15,055 | 17,591 |
Sweeteners | 5 | 13 |
Spices | 199 | 194 |
Stabilizers | 30 | 50 |
Extracts | 8 | 8 |
Frozen Fruit | 100 | 312 |
Dehydrated Fruit | 50 | 92 |
Stabilized Fruit | 160 | 302 |
Frozen Cookies | 2,484 | 659 |
Mole Crackers | 910 | 2,314 |
Jellies | 74 | 100 |
Coconut Oil | 56 | 149 |
Gelatin | 100 | 160 |
Flour | - | - |
Syrups | 262 | 218 |
Liquid Lemon Juice | 100 | 95 |
Powered Lemon Juice | 2 | 2 |
Milk and Milk Products | 1,448 | 1,936 |
Vegetable Shortening | 30 | 33 |
ADB Mixtures | 639 | 544 |
Monoglyceride | 6 | 9 |
Mustard | 1,260 | 1,280 |
Ground Mustard | - | - |
Nut | 25 | 32 |
Oleoresin | 37 | 37 |
Coconut Paste | - | - |
Tomato Paste | 19,740 | 17,395 |
Pectin | 24 | 26 |
Cucumber Bites | 100 | 99 |
Peppers | 121 | 111 |
Polydextrose | 186 | 189 |
Vitamin Premixtures | 21 | 24 |
Vegetable Protein | 205 | 185 |
Chemicals | 679 | 617 |
Ice Cream Flavors | 278 | 35 |
Dry Flavors |
| 300 |
Refined Salt | 6,238 | 6,277 |
Salts | 67 | 10 |
Wheat Bran | 586 | 537 |
Seasonings | 12 | 36 |
Seeds and Cereals | 107 | 256 |
Semolina | 73,641 | 73,534 |
Textured Soy | 60 | 87 |
Tea | 120 | 87 |
Toppings | 103 | 328 |
ADB Sales - Chile Peppers | 13 | 14 |
ADB Sales - Ground Mustard | 720 | 662 |
ADB Sales - Peppers | 92 | 76 |
Vinegar | 2,581 | 2,902 |
Vitamins and Minerals | 0 | - |
Egg Yolk | 10,347 | 10,802 |
Powdered Egg Yolk | 1 | 0 |
Megamex Salsa Project |
| 87 |
Wonka Projects |
| 75 |
Total | 261,979 | 268,494 |
|
|
|
Agricultural Raw Materials | ||
Tomato for puree | 46,342 | 57,434 |
Tomatillo for salsa | 3,149 | 3,536 |
Jalapeño chili pepper | 3,795 | 3,449 |
Onion | 272 | 309 |
Carrot | 3,135 | 2,727 |
Sweet yellow corn | 21,613 | 17,050 |
White corn | 345 | 291 |
Chickpea | 133 | 128 |
Potato | 694 | 589 |
Green bean | 435 | 307 |
Dry chipotle pepper | 522 | 486 |
Tomato for salsa | 11,712 | 10,205 |
Tomatillo for salsa | 8,192 | 8,649 |
Onion | 3,155 | 3,027 |
Jalapeño chili pepper | 1,904 | 1,774 |
Cilantro | 424 | 380 |
Prickly pear cactus | 2,829 | 2,813 |
Ancho chile pepper | 701 | 688 |
Pasilla chile pepper | 701 | 653 |
Sesame | 1,699 | 1,643 |
Peanut | 1,329 | 1,214 |
Pumpkin seed | 279 | 209 |
Serrano chili pepper | 42 | 67 |
Avocado pulp | 497 | 547 |
Chipotle chili pepper | 42 | - |
Fresh ancho chili pepper | 2,036 | 1,695 |
Fresh pasilla chili pepper | 1,351 | 2,456 |
Frozen whole strawberries 27+1 | 1,139 | 1,088 |
Frozen sliced strawberries 27+1 | 1,192 | 1,068 |
Frozen sugarless strawberry puree | 470 | 997 |
Whole blackberries 4+1 | 270 | 343 |
Whole sugarless blackberries | 2 | 13 |
Blackberry puree 4+1 | 128 | 267 |
Ground pineapple 4+1 | 102 | 177 |
Frozen apricot chunks with sugar | - | 161 |
Whole raspberries 4+1 | 4 | 8 |
Raspberry puree 4+1 | 6 | 8 |
Sugarless rasberry puree | 0 | 6 |
Apple chunks 4+1 | - | - |
Standardized sliced strawberries | - | 25 |
Orange strips | - | 10 |
Strawberry seed | 7 | 11 |
Grape Concentrate | 1 | 6 |
Mango chunks | - | 10 |
Aseptic apple pulp | 8 | 19 |
Hawthorn puree | 1 | 22 |
Peach chunks 4+1 | 12 | - |
Peach pulp 4+1 | - | 10 |
Coastal honey | 958 | 1,337 |
Highland honey | 286 | 544 |
Chamomile tea | 543 | 728 |
Lemon tea | 126 | 273 |
Mint tea | 64 | 109 |
7 Blossom tea | 30 | 59 |
Hibiscus tea | 27 | 28 |
Linden tea | 45 | 15 |
Total | 122,752 | 129,666 |
Total MP + MPA | 384,730.46 | 398,159.57 |
Renewable material: renewable materials from abundant sources that are quickly replaced during ecological cycles or agricultural processes, in such a way that these and other related resources are not threatened and will be available for the next generation.
* Due to the traceability and effectiveness of the measurement of our packaging materials based on the number of resources and different purchasing units, starting in 2017, there is no report for the total volume of packaging material used.
IP-4. Environmental investments
Line item | Monetary Investment | Percentage | Description | ||
2017 | 2018 | 2017 | 2018 | ||
Reduced Carbon Footprint | $ 485,600.24 | $ 389,480.50 | 1% | 1% | Investment made for the Organizational Life Cycle Assessment (OLCA), which determines the carbon footprint for the Company’s main product categories |
Reduction of CO2 emissions (reduction of air emissions) | $ 8,088,622.98 | $ 2,014,169.43 | 18% | 6% | Investment made by the Group’s facilities to treat air emissions (installation/maintenance of anti-pollution equipment) |
Reduction of Water Emissions (waste water treatment) | $ 20,230,484.27 | $ 12,846,028.16 | 44% | 41% | Investment in waste water treatement systems at Group facilities |
Reduction of GHG emissions | $ - | $ - | 0% | 0% | No evidence of investments to reduce GHG emissions |
Reduction of Waste (post-Industrial waste handling) | $ 8,112,381.43 | $ 8,381,882.47 | 18% | 27% | Total cost of adequate disposal of non-valued waste |
External Consulting Services | $ 1,888,137.50 | $ 1,668,110.43 | 4% | 5% | This cost includes:a) External environmental management servicesb) External certifications in environmental compliancec) Consulting services for developing the Environmental Management System (SiGA) model |
Anti-Pollution Equipment | $ 154,828.92 | $ 156,105.52 | 0% | 1% | Investments in anti-pollution equipment (PTAR, PTAN, gas scrubbers, sludge trap, filter press, dust extraction, etc.) and other projects for environmental purposes |
Green Purchases | $ 15,400.00 | $ 101,550.00 | 0.03% | 0.3% | Expenses incurred for ecological purchases and/or development of environmental awareness events |
Post-Consumer Waste Management | $ 529,316.76 | $ 535,339.09 | 1% | 2% | Total cost for integrated post-consumer PET waste management, implemented through ECOCE for collection, valuation and integration into new production chains (circular economy) |
Participation in Industrial Organizations and in Environmental Sustainability Fora | $ 265,238.18 | $ 369,694.94 | 1% | 1% | Payments to environmental associations, conferences, participation in trade fairs or expos, various fees, etc. |
Hiring specific personnel | $ 525,469.97 | $ 2,299,433.45 | 1% | 7% |
|
Other Items | $ 5,798,084.28 | $ 2,371,222.43 | 13% | 8% |
|
ANNUAL TOTAL | $46,093,564.53 | $ 31,133,016.42 | 100% | 100% |
|
* The reported information only includes the amounts reported by the Group’s facilities as environmental investments for environmental control and management in their processes. It also includes the amounts that the Environmental Sustainability department allocates for the payment of various environmental activities that it carries out.
** The information does not include data from the CAPEX investments that the Group makes for large-scale projects.
308-1. New suppliers that were screened using environmental criteria
In 2018, we did not audit new suppliers; however, the traceability of our raw materials and our relationship with our suppliers is essential to guaranteeing that our products reach our consumers’ tables with the quality we are known for.
That is why, regardless of the type of product or service they offer, all of our suppliers must sign and conform to the Code of Conduct for Suppliers, which describes the minimum social and environmental requirements they must meet, and evaluates their compliance with labor standards and current environmental legislation. In 2018, 175 new suppliers signed the Code.Agricultural Sustainability Plan:
Through the Good Practices Manual, training sessions and environmental audits, we support our agricultural suppliers in their adoption of best labor and environmental practices. In 2018, we held two training sessions:
Topic | Location | Number of Suppliers Trained |
Integrated Crop Management | Los Mochis and San Luis Potosí | 39 |
Agricultural Sustainability Workshop | Los Mochis and San Luis Potosí | 43 |
Audits
In order to provide continuity and validity to our progress in the Agricultural Sustainability Plan, we have a team of six internal auditors who evaluate and monitor the status of the properties. They monitor whether the suppliers are located in environmentally sensitive areas and the measures that are being implemented to protect them, as well as the measures adopted to improve soil quality, increase recycling and reduce waste production. They do this using a checklist that measures progress and improvement points for each supplier.
Our auditors have the Produce Safety Alliance certification.
The producers are audited based on the guidelines contained in the Good Hygiene Practices Manual for Agricultural Products, with two main criteria: Good Agricultural Practices Manual and the Agricultural Sustainability Program.
In 2018, 38 suppliers were evaluated against the Good Agricultural Practices criteria and 37 against the Agricultural Sustainability Program criteria.306-2. Waste by type and disposal method
Total weight of waste generated, by type
Type | 2018 | 2017 |
(Tons) | (Tons) | |
Hazardous waste | 90 | 133 |
Non-hazardous waste (except waste water) | 34,142 | 36,722 |
Total waste generated | 34,231 | 36,855 |
Total weight of waste generated, by elimination method
Elimination Method | 2018 | 2017 |
(Ton) | (Ton) | |
Recycling | 49 | 61 |
Other (final disposal) | 41 | 73 |
Total | 90 | 134 |
Total weight of non-hazardous waste, by elimination method
Elimination Method | 2018 | 2017 |
(Ton) | (Ton) | |
Recycling | 23,867 | 27,183 |
Other (Landfill: includes special handling waste and non-valued urban solid waste) | 10,275 | 9,540 |
Total | 34,142 | 36,723 |
Total weight of waste generated, during the last 4 years
Discarded Waste (incinerated, landfill) | Unit | Year 2018 | Year 2017 | Year 2016 | Year 2015 |
Total waste | Metric tons | 34,231 | 36,856 | 40,999 | 30,596 |
Scope of information | % | 85 | 85 | 85 | 85 |
Despite the fact that certain Plants established waste reduction goals, environmental goals were not established for the Group nor by Division. With the SDG strategic alignment, our short-term objective is to establish goals.
306-1. Water discharge by quality and destination
Discharge streams (water discharge) | Volume (m3) | ||
2018 | 2017 | 2016 | |
Discharge into federal drainage | 513,425.00 | 500,595 | 217,559 |
Discharge into municipal network | 284,879.58 | 515,939 | 428,167 |
Discharge into subsoil | 66,514.84 | 70,109 | 76,513 |
Total | 864,819.42 | 1,086,643 | 722,239 |
The treated waste water is discharged into federal and municipal receiving bodies of water and complies with the maximum permissible limits established in the corresponding Official Mexican Standards (NOM-001-SEMARNAT-1996 and NOM-002-SEMARNAT-1996).
The Grupo Herdez treatment plants are specifically designed for each facility, thereby ensuring the appropriate treatment of water used in processing and sanitation.
In 2018, the Mexico Plant donated very small amounts of treated waste water to the Municipal Government of Cuautitlán.
Quality of Discharged Water
In 2018, the estimated quantities of discharge in waste water that was treated at Grupo Herdez, expressed in tons, were:
FAT, OIL AND GREASE: 5.78 (Ton)
DBO: 57.59 (Ton)
DQO: 213.58 (Ton)
SST: 25.98 (Ton)
SDT: 119.65 (Ton)
SS: 0.20 (Ton)
305-7. Nitrogen oxides (NOx), sulfur oxides (SOx), and other significant air emissions
Atmospheric Emissions | 2018 (Ton) |
NOx | 858.77 |
POG (Persistent Organic Pollutants) | - |
VOC (Volatile Organic Compounds) | 0.55 |
HAP (Hazardous Air Pollutants) | - |
PM (Particulate Matter) | - |
OTHERS: | - |
CO | 34.49 |
PS | 2.26 |
COT | 2.51 |
SO2 | 4,284.78 |
SO3 | 0.82 |
SOx | 4,285.60 |
Filterable PS | 6.34 |
NMVOCs | 0.41 |
The methodology used is one of direct determination, which uses specific emission factors for each type of pollutant, as recommended by the Greenhouse Gas Protocol (GHGP) for emissions from direct sources, both fixed (stationary) and mobile.
To determine the emission factors to be used, we took into consideration the provisions established by the UK Deparment for Environment, Food and Rural Affairs (DEFRA), the US Environmental Protection Agency (EPA) and the Intergovermental Panel on Climate Change (IPCC) 2006 Guidelines for National Greenhouse Gas Inventories, through the Mobile Combustion GHG Emissions Calculation Tools and the Stationary Combustion GHG Emissions Calculation Tools. The above may be consulted at the GHG Protocol Website.
On the other hand, although the data represent the Group in aggregate, the estimate is based on specific data provided by each facility, taking into consideration fuel consumption - measured directly - in fixed and mobile sources at Grupo Herdez. Likewise, we used conversion factors for units based on the metric decimal system for the conversion of kilograms to tons.305-6. Emissions of ozone-depleting substances (ODS)
Grupo Herdez does not produce, import or export CFC-11 (R-11) and R-14 and R-22 class substances.
The coolants that are most used are R-410A, R-134A, R-407C, R-404A, R-507, R-147, R-427 and R-MO99. In 2016, we launched a new campaign to substitute and erradicate this type of substance. In 2019, some facilities were still implementing their substitution plan for the R-22 coolant to eliminate its use within the company.
305-5. Reduction of GHG emissions
Reduction of GHG emissions (Tm CO₂ eq.) | 2018 |
Redesign of processes | 674.19 |
Equipment conversion and adaptation |
|
Fuel substitution |
|
Change in employee behavior |
|
Others (saving actions in consumption equipment) | 4,349 |
Total | 5,023 |
Note 1: The gases included in the calculation were CO₂, CH₄ and N₂O.
Note 2: The reductions were manifested in Scope 1 and in Scope 2.
The information was estimated based on a comparative analysis of the years 2018 vs. 2017. The criteria to determine energy savings compared consumption in (kW/h -electrical power- or m3 -fuel-) per ton produced. No specific base year or baseline has been established.
All of the emissions reported were estimated using emission factors corresponding to each type of energy.
305-4. GHG Emissions Intensity
Taking into consideration the emissions from the Plants, Cedis and Tuna Fleet and at t the same time, including direct (mobile and fixed source) and indirect emissions (electrical power from non-renewable sources), the GHG emissions intensity in 2018 is 0.193 tons of CO2e/tons produced. In 2018, intensity was 0.198, representing a reduction of approximately 0.3%.
The intensity of GHG emissions is expressed in tons of CO2e per tons produced and is expressed based on the sum of direct and indirect emissions reported in previous emissions indicators, adding the emissions from fuel consumption and the emissions from electrical power supplied by the CFE network.
Note: The gases included in the calculation were CO₂, CH₄ and N₂O.
305-2. Direct (Scope 2) GHG emissions
Indirect Emissions | |||
Type | 2018 | 2017 | 2016 |
Ton CO2 eq | Ton CO2 eq | Ton CO2 eq | |
Indirect Emissions | 25,929 | 33,899 | 21,684 |
Note: The gases included in the calculation were CO₂, CH₄ and N₂O.
In terms of GHG emissions from direct sources (fixed and mobile - due to the use of fuel-), currently there is no single base year; the indicators are compared each year using the previous year as a reference.
The estimated emissions were for CO2eq (taking the calculation of the CO2, CH4 and N2O emissions as a basis, as well as their heating power based on the GHG-PI). We also used the new emission factors recommended by SEMARNAT in December 2014.
For indirect sources, the emission factor was taken from the report issued in February 2019 by the Federal Electricity Commission (CFE). The emission factors for Marine Diesel (mobile source) and Aviation Fuel for mobile sources were taken from the factors listed in the Good Practice Guidance and Uncertainty Management in National Greenhouse Inventories (GPGUMNGI, 2000) issued by the IPCC for mobile sources, based on recommendations in international standards. The heating power was taken from specifications provided by the Mexico GHG Program, which recommends using data from the PCG-GHG (Greenhouse Gas PROTOCOL INITIATIVE), version AR5. Emission factors for Gasoline, LP gas and Diesel for mobile sources are values suggested by the IPCC calculation tools (GREENHOUSE GAS PROTOCOL INITIATIVE-WRI-), as recommended by international standards and which are recommended by the methodology in the Mexico GHG Program.
305-1. Direct (Scope 1) GHG emissions
Direct Emissions from fuel consumption in fixed sources | |||
Fuel | 2018 | 2017 | 2016 |
Ton CO2 eq | Ton CO2 eq | Ton CO2 eq | |
Natural Gas | 12,525 | 13,944 | 14,684 |
Fuel Oil | 19,820 | 20,649 | 19,128 |
Industrial Diesel | 178 | 178 | 215 |
LP Gas | 3,294 | 3,352 | 3,986 |
Gasoline | - | - | - |
Subtotal | 35,817 | 38,123 | 38,012 |
|
|
|
|
Direct Emissions from fuel consumption in mobile sources | |||
Fuel | 2018 | 2017 | 2016 |
Ton CO2 eq | Ton CO2 eq | Ton CO2 eq | |
LP Gas | 1,324 | 1,038 | 1,144 |
Marine Diesel | 31,782 | 35,259 | 36,161 |
Conventional Diesel | 37 | 16 | 57 |
Gasoline | 265 | 320 | 369 |
Aviation Fuel | 687 | 599 | 790 |
Subtotal | 34,096 | 37,231 | 38,521 |
Total Direct Emissions | ||
2018 | 2017 | 2016 |
69,913 | 75,353 | 76,533 |
Note: The gases included in the calculation were CO₂, CH₄ and N₂O.
Grupo Herdez has not determined biogenic CO2 emissions for any type of waste or biomass that is produced, since the waste is not sent for incineration and is also not used as alternative fuel in our Plants.
In terms of GHG emissions from direct sources (fixed and mobile – due to the use of fuel –), currently there is no single base year; the indicators are compared each year using the previous year as a reference.
For direct and indirect sources, direct estimation methodology was used by applying emission factors that are established in internationally renowned sources, some of them adopted by the SEMARNAT. Due to the units in which they are expressed, the factors are directly applied to the consumption of each energy source reported to estimate the tons of CO2e. Each determination worked under the assumption that Grupo Herdez does not record direct or accidental emissions or releases (whether they are leaks or spills) of HFC, PFC, SF6 and/or NF3, which may be considered part of its atmospheric emissions.
For direct sources (fixed and mobile), the emission factors were taken from the GHG-PI version 4.0 (fixed sources) and 2.3 (mobile sources).
303-5. Water consumption
Source | 2018 | 2017 | 2016 | |||
Total Volume (Ml) | Volume in Water Stressed Areas | Total Volume (Ml) | Volume in Water Stressed Areas | Total Volume (Ml) | Volume in Water Stressed Areas | |
Rivers, lakes | 160.5 | 161 | 686.2 | 717.0 | ||
Underground (wells) | 419.8 | 361 | 854.9 | 668.7 | 833.7 | 649.2 |
Seas, oceans | - | - | - | - | ||
Municipal network | 4.9 | 10.3 | 2.5 | 12.0 | 2.7 | |
Waste water from other organizations | - | - | - | - | ||
Other | 22.4 | 12 | 26.9 | 26.9 | 26.0 | 26.0 |
Total | 608 | 534 | 1,578 | 698 | 1,589 | 754 |
| 2018 Total Volume (Ml) | 2017 Volume (Ml) | 2016 Volume (Ml) |
Rainwater (captured and stored directly by the organization) | 76 | 76 | 76 |
The reported consumption is measured directly using measurement instruments that are monitored, with some of them certified by federal, state and municipal authorities. The consumption is reported to those authorities using various formats and reporting mechanisms.
The rainwater volume is an estimate of the volume recovered at the Duque de Herdez Complex, Mexico Plant, and Cedis México, which is used to water their gardens.
Note: Since we are not using rainwater within production processes, it is reported separately.
303-4. Water discharge
Discharge by Source
Source of Discharge | Volume | Unit | ||
2018 | 2017 | 2016 | ||
Rivers, lakes (federal bodies) | 513 | 501 | 218 | Ml |
Underground (wells) | - | - | - | Ml |
Seas, oceans | - | - | - | Ml |
Municipal network (municipal drainage) | 285 | 516 | 428 | Ml |
Rainwater | - | - | - | Ml |
Water discharged from other organizations | - | - | - | Ml |
Other (subsoil) | 67 | 70 | 77 | Ml |
Total | 865 | 1,087 | 722 | Ml |
Note: A summation is made of discharge by primary source; in terms of the facilities, they have two sources of water discharge.
Discharge by Water Type
| 2018 | 2017 | 2016 | |||
Total Volume (Ml) | Volume in Water Stressed Areas | Total Volume (Ml) | Volume in Water Stressed Areas | Total Volume (Ml) | Volume in Water Stressed Areas | |
Fresh water (≤1,000 mg / l of total dissolved solids) | - | - | - | - | - | - |
Other water (≤1,000 mg / l of total dissolved solids) | 865 | 743 | 1,087 | ND | 722 | ND |
Note: Fresh water includes any source of extraction, except for water tank trucks, which are included in “other water”.
Priority substances of concern for water discharge
Substance | Method for Determining Its Importance (International Standard, Authorized List, or Criterion Used) |
Biochemical Oxygen Demand (BOD) | Compliance with national standards and specific discharge conditions established by the Mexican Government |
Total Suspended Solids (TSS) | |
Total Dissolved Solids (TDS) | |
Sedimentable Solids (SS) | |
Hydrogen Potential (HP) | |
Electrical Conductivity (EC) | |
Temperature | |
Fat, Oil and Grease (FOG) | |
Chemical Oxygen Demand (COD) | Standard determined for the operational control of the system |
The standards implemented at Grupo Herdez facilities in compliance with the discharge limits set for priority substances are:
- NOM-001-SEMARNAT-1996: Establishes the maximum permissible limits for pollutants for discharging waste water into national waters and assets- NOM-002-SEMARNAT-1996: Establishes the maximum permissible limits for pollutants when discharging waste water into urban or municipal sewer systems- State Technical Standard NTE-SLP-AR-001/05: Establishes specific conditions for discharging waste water into the drainage network and sewer system in the municipalities of San Luis Potosí, Soledad de Graciano Sánchez and Cerro de San Pedro.- Specific Discharge Conditions: Established by federal authorities pursuant to Article 140 of the Law on National Waters and its Regulations, which states that in order to determine the specific discharge conditions, “The Commission” shall take into account the parameters and maximum permissible limits contained in the Official Mexican Standards issued by the competent authorities on wast water discharge and treatment of water for use or human consumption, as well as the parameters and maximum limits established in the Statements on the Classification of National Bodies of Water that are published in the provisions of Article 87 of said “Law”.In 2018, two incidents arose resulting from non-compliance with the discharge limits at the Celaya Plant based on Official Mexican Standard (NOM-001-SEMARNAT-1996), due to failure to comply with the Biochemical Oxygen Demand (BOD) parameter.
303-3. Water withdrawal
Source | 2018 | 2017 | 2016 | |||
Total Volume (Ml) | Volume in Water Stressed Areas | Total Volume (Ml) | Volume in Water Stressed Areas | Total Volume (Ml) | Volume in Water Stressed Areas | |
Rivers, lakes | 657 | 657 | 686 | 686 | 717 | 717 |
Underground (wells) | 777 | 598 | 855 | 669 | 834 | 649 |
Seas, oceans | ||||||
Municipal network | 7.3 | 2.4 | 10.3 | 2.5 | 12.0 | 2.7 |
Waste water from other organizations | - | - | - | - | - | - |
Other | 22 | 22 | 27 | 27 | 26 | 26 |
TOTAL | 1,464 | 1,279 | 1,578 | 1,385 | 1,589 | 1,395 |
The extraction volumes of underground water, surface water, from the municipal network and waste water from other organizations are the result of direct measurements with meters installed in the Plants and Distribution Centers. Another primary source of information are the invoices paid for consumption or water supply services. Rainwater consumption is the only metric that is estimated with the assistance of data on the rainwater storage capacity at the installations, the length of use and the capacity of the pumps that are used.
303-2. Management of water discharge-related impacts
The minimum established standards for the quality of effluent discharge at Grupo Herdez are:
Standard | Method of determination (for facilities without specific discharge requirements) | Standard or Internal Quality Guide | Specific Sector Standard |
Biochemical Oxygen Demand (BOD) | Not Applicable | Not Applicable | .- NOM-001-SEMARNAT-1996,.- NOM-002-SEMARNAT-1996,.- State Technical Standard: NTE-SLP-AR-001/05.- Specific Discharge Conditions |
Total Suspended Solids (TSS) | Not Applicable | Not Applicable | |
Total Dissolved Solids (TDS) | Not Applicable | Not Applicable | |
Sedimentable Solids (SS) | Not Applicable | Not Applicable | |
Hydrogen Potential (HP) | Not Applicable | Not Applicable | |
Electrical Conductivity (EC) | Not Applicable | Not Applicable | |
Fat, Oil and Grease (FOG) | Not Applicable | Not Applicable | |
Chemical Oxygen Demand (COD) | Not Applicable | Spectophotometry Method | Not Applicable |
* NOM-001-SEMARNAT-1996; Establishes the maximum permissible limits for pollutants for discharging waste water into national waters and assets | |||
* NOM-002-SEMARNAT-1996; Establishes the maximum permissible limits for pollutants when discharging waste water into urban or municipal sewer systems | |||
* State Technical Standard: NTE-SLP-AR-001/05 establishes specific conditions for discharging waste water into the drainage network and sewer system in the municipalities of San Luis Potosí, Soledad de Graciano Sánchez and Cerro de San Pedro. | |||
*Specific Discharge Conditions: Established by federal authorities pursuant to Article 140 of the Law on National Waters and its Regulations.
|
303-1. Interactions with water as a shared resource
Water withdrawal
Source | Withdrawal Method | Location and Name of Body of Water | * Description of Related Impacts |
Rivers, lakes | Pumping | Canal Lateral 18+420, from the Valle del Fuerte canal, Ahome, Sin. | Possible resource depletion |
Seas, oceans | Not Applicable | Not Applicable | Not Applicable |
Underground (wells) | Pumping | 1. San Luis Potosí, SLP/ San José - Los Pilares Dam basin and others2. Villagrán, Gto. /Laja River basin3. Tapachula, Chis. /Suchiate River basin and others4. Cuautitlán, Edo. Mex. /Mexico Valley Basin5. Lagos de Moreno, Jal. /Santiago River Basin6. Umán, Yuc. / Yucatan Peninsula basin | Possible resource depletion |
Municipal network | Pumping | The locations of the facilities that receive water from the municipal network are:1. San Luis Potosí, SLP2. Tijuana, Baja California3. Monterrey, Nuevo Leon4. Guadalajara, Jalisco5. Tapachula, Chiapas | Possible resource depletion |
Rainwater (captured and stored directly by the organization) | Pumping | 1. Duque de Herdez Industrial Complex, San Luis Potosí, SLP2. Mexico Plant, Cuautitlán, State of Mexico3. Mexico Distribution Center, Cuautitlán, State of Mexico | Not Applicable |
Waste water from other organizations | Pumping | Treated water from Herdez, S.A. de C.V. (Mexico Plant, and CEDIS, Mexico) Cuautitlán, State of Mexico | Not Applicable |
Other | Pumping | Valle de Chalco, State of Mexico | Possible resource depletion |
Note: Waste water from other organizations - a Company Name owned by Grupo Herdez is listed as a supplier of treated waste water. It records discharged waste water and transfers the treated water to CEDIS Mexico for watering green spaces. |
Consumption
Source | Use of Extracted Water | Consumption Location | * Description of Related Impacts |
Rivers, lakes | Production, auxiliary services and sanitation services | Ahome, Sinaloa | Possible resource depletion |
Seas, oceans | Not Applicable | Not Applicable | Not Applicable |
Underground (wells) | Production, auxiliary services and sanitation services | 1. San Luis Potosí, SLP2. Cuautitlán, State of Mexico3. Villagrán, Guanajuato4. Tapachula, Chiapas5. Lagos de Moreno, Jalisco6. Umán, Yucatán | Possible resource depletion |
Municipal network | Production, auxiliary services and sanitation services | 1. San Luis Potosí, SLP2. Tijuana, Baja California3. Monterrey, Nuevo Leon4. Tlaquepaque, Jalisco5. Tapachula, Chiapas | Possible resource depletion |
Rainwater (captured and stored directly by the organization) | Watering green spaces | 1. San Luis Potosí, SLP2. Cuautitlán, State of Mexico | Not Applicable |
Waste water from other organizations | Watering green spaces and sanitation services | Cuautitlán, State of Mexico | Not Applicable |
Other | Production, auxiliary services and sanitation services | Valle de Chalco, State of Mexico | Possible resource depletion |
Water discharge
Source | Discharge Method | Discharge Destination | * Description of Related Impacts |
Rivers, lakes | Gravity and direct transfer to drainage or receiving body of water | Federal receiving body of water | Pollutant discharge into receiving body of water |
Seas, oceans | Not Applicable | Not Applicable | Not Applicable |
Underground (wells) | Gravity and direct transfer to drainage or receiving body of water | Federal receiving body of water, municipal sewage | Pollutant discharge into receiving body of water |
Municipal network | Gravity and direct transfer to sewer or receiving body of water | Municipal sewage | Pollutant discharge into receiving body of water |
Rainwater (captured and stored directly by the organization) | Pumping | Federal receiving body of water | Possible pollutant discharge into receiving body of water |
Waste water from other organizations | Pumping | Federal receiving body of water | Pollutant discharge into receiving body of water |
Other | Pumping | Municipal sewage | Pollutant discharge into receiving body of water |
Note: The quality of the wastewater discharge that is sent to the receiving bodies of water is monitored through compliance with the maximum permissible limits established in the corresponding Official Mexican Standards. |
Basins where water is extracted for the organization:
Basin | * Description of Related Impacts |
San Luis Potosí, SLP/ San José - Los Pilares Dam basin and others | Possible resource depletion |
Laja River | Possible resource depletion |
Suchiate River and others | Possible resource depletion |
Valley of Mexico | Possible resource depletion |
Santiago River | Possible resource depletion |
Yucatan Peninsula | Possible resource depletion |
Related Impacts
Currently, we intend to maintain and improve current water measures, in addition to including new measures that will allow us to provide valuable information in order to detect new opportunities. Likewise, we seek to promote awareness among our employees and suppliers through training sessions for better resource management.
We are aware that water is an essential element and is fundamental to Grupo Herdez operations. That is why we seek to maintain and improve current water measures, in addition to including new measures, over the short-term, that will allow us to provide valuable information in order to detect new opportunities. Likewise, we promote awareness among our employees and suppliers through training sessions for better resource management.
Our water-related objectives are established based on water consumption and wastewater discharge indicators that are recorded at each facility. Each facility identifies areas of opportunity in their processes and produces estimates about the possible savings that each one may provide, to subsequently propose an annual attainable goal. Currently, those goals bear no relation to the local context of their locations.
We do not apply an analytical, holistic, or deep approach to identify the possible impacts. Rather, we intuitively consider the possible impacts that could be caused by the consumption volumes of water that are extracted at the sources, and by the quantity of pollutants that are present in the waste water that is discharged into the different receiving bodies of water.
302-4. Reduction of energy consumption
Reduction initiatives | 2018 | 2017 |
Energy Saved (GJ) | Energy Saved (GJ) | |
Redesign of processes | 45,918 |
|
Equipment conversion and adaptation | 12,521 |
|
Changes in employee behavior |
|
|
Others (saving actions in consumption equipment) | 13,215 | 25,573 |
Total | 71,654 | 25,573 |
The savings from redesign of the processes in 2018 includes electrical power and fuel such as natural gas, Fuel Oil and LP gas. Savings in 2017 only includes electrical power.
The information on saved energy was obtained from a comparative analysis of the years 2017 vs. 2016 and 2018 vs. 2017. The savings criteria were the comparison of consumption in (kW/h -electrical power- or m3 -fuel-) per ton produced. No specific base year or baseline has been established.
The sources that were consulted are related to the conversion factors used and calorific value of the fuels.
- The conversion factors expressed as GJ/m3 were taken directly from the GHG Reporting Protocol, version 1.0, September 2006, Thermal Units.- National Energy Balance 2011, Ministry of Energy; Converting Units of Energy.- Market Outlook for Liquified Petroleum Gas 2012 - 2026, Ministry of Energy.302-3. Energy intensity
In terms of electric power consumption, energy intensity in 2018 was 154.25 kWh/ton produced, which was 1.5% lower than the previous year.
In 2017, we consumed 80,583,929 kWh to produce 512,509.73 tons, while in 2018, we consumed 78,954,927 kWh to produce 544,989 tons.
In terms of fuel consumption, energy intensity in 2018 was 12.27 m3/ton produced, which was 9.6% lower than the previous year.
The Group’s total energy intensity in GJ/ton produced was 2.51, which was 3.4% lower than the previous year.
GJ/ton produced | |
2018 | 2.51 |
2017 | 2.60 |
2016 | 2.68 |
This includes the sum of electric power sourced by the Federal Electricity Commission (CFE) and energy from the wind project.
Note: Energy intensity is expressed based on tons produced; in the case of units expressed as kW/h/ton produced, electric power consumption and fuel consumption is reported separately. In the second case, althouth the sum total of fuel includes consumption by the tuna fleet and the distribution centers, energy intensity is calculated only from the sum of the production from all of the plants, since the fleet and the distribution centers do not manufacture finished products.
In the case of total energy intensity expressed in GJ/ton, both consumption types (electric power and fuel consumption) are standardized in thermal units.
302-1. Energy consumption within the organization
Type of Fuel | 2018 | 2017 | 2016 |
Non-Renewable Sources | (GJ) | (GJ) | (GJ) |
Diesel | 3,043 | 2,786 | 3,918 |
Cleanbustoleo | - | 2,576 | - |
Fuel Oil | 226,440 | 269,432 | 272,186 |
Gasoline | 3,938 | 4,847 | 5,592 |
LP Gas | 74,818 | 72,583 | 85,101 |
Natural Gas | 258,426 | 264,713 | 278,759 |
Marine Diesel | 380,137 | 421,725 | 432,513 |
Aviation Fuel | 9,915 | 8,639 | 11,399 |
Total Non-Renewable Sources | 996,717 | 1,044,725 | 1,089,468 |
Type of Fuel | 2018 | 2017 | 2016 |
Renewable Sources | (GJ) | (GJ) | (GJ) |
Biodiesel | 1,202.72 | 2,575.88 | N/A |
Total Renewable Sources | 1,202.72 | 2,575.88 | N/A |
Total fuel consumption | 997,920 | 1,049,878 | 1,089,468 |
Total 2018 | GJ | kWh |
Electricity consumption | 284,215 | 78,948,544 |
Heating consumption | ND | ND |
Cooling consumption | ND | ND |
Steam consumption | ND | ND |
The total energy consumption in 2018 was 1,282,135 GJ, including fuel and electric power. Electricity consumption is equivalent to 78,954,927 kWh of electrical power.
Our calculation methodology is based on converting m3 of fuel consumption into units of heat (Gigajoules) and from the kWh of electric power consumed into Gigajoules using national conversion factors. For the Tuna Fleet, we included data from fuel and electrical power. It also includes the conversion of the electric power data from kWh to MWh.
Note: In 2018, due to operational issues, the Cedis began to report their production in displaced tons instead of invoiced tons, in order to make the environmental performance indicators more representative of their operations.
103-13. Management approach
Grupo Herdez knows that we must identify the main impacts and risks that may affect the continuity and trascendency of our operations. Therefore, agents of change are present in each of our business units. In coordination with other company departments and our stakeholders, they design strategies, directives and policies that focus on producing actions that take care of and protect the environment. In this way, we are able to create a culture of respect, care, and synergy that allows us to overcome social, political and climate changes that we face every year.
That is why we are perfecting our strategy and we present the alignment of our four action pillars with 7 Sustainable Development Goals. They allow us to highlight our environmental priorities: Clean water and sanitation, Responsible Consumption and Production, Climate Action and Life Below Water.

Likewise, in 2017 and 2018, we identified environmental aspects and impacts for the Plants, Cedis and Tuna Fleet, in order to gather the elements to develop an Environmental Management System to be implemented starting in 2019.
205-2. Communication and training about anti-corruption policies and procedures
In 2018, 129 employees received training about topics on the fight against corruption. Likewise, the 9 Members of the Board were informed regarding the policies and prodedures to fight against corruption.
To cap off the reinforcement campaign for the Code of Ethics, 97 non-unionized employees and 9 Members of the Board of Directors (100% of the Members of the Board) reinforced their knowledge about each of the points of the Code, including anti-corruption and human rights violations. We also held various training and communication courses in 2018, which included:
- Workshop: “Promoting a Culture of Legality in the Workplace” This activity forms part of our business strategy to reinforce Ethical Culture, in order to strengthen the Culture of Legality among all employees at Grupo Herdez. The workshop was taught by internal trainers who are accredited on the topic of Legality. It was attended by 20 employees from the four corporate offices located in Mexico City.
- Online training: “Intelligence and Prevention of Unlawful Transactions: Money Laundering, Fraud and Corruption” taught by PricewaterhouseCoopers to employees from specific departments that are responsible for risk prevention. Information sharing is divided into two stages. In the first stage, material was shared via e-mail to 13 employees in the Marketing and Business Departments and in the Plant. In the second stage, it was shared via e-mail to 8 employees in the Purchasing and Procurement Department.
- Reinforcing the Code of Ethics, targeting personnel from different departments, with 97 employees participating This reinforcement takes place through one-hour, in-person training sessions.
- Course: “Practical Applications of the Code of Ethics for Public Accountants to Prevent Company Fraud” taught by the Instituto Mexicano de Expansión Fiscal y de Negocios, S.C., with the assistance of a Grupo Herdez employee.
205-1. Operations assessed for risks related to corruption
The Office of Human Resources, in conjunction with the Internal Audit Department, are responsible for monitoring all reports of non-compliance with the Code of Ethics, including complaints and reports related to corruption, human rights violations and money laundering. Once the priority topis have been identified, the Office of Human Resources and Compliance establish measures to reduce and prevent these types of practices.
Currently, we do not perform a formal risk analysis on these topics; however, monitoring makes it possible to detect higher-frequency incidents, such as abuse of trust, giving preference to suppliers, unlawful payments and acceptance of bribes.
Through training courses and communication tools within the plants and corporate offices, various actions were implemented in 2018:
- Workshop: “Promoting a Culture of Legality in the Workplace” This activity forms part of our business strategy to reinforce Ethical Culture, in order to strengthen the Culture of Legality among all employees at Grupo Herdez. The workshop was taught by internal trainers who are accredited on the topic of Legality. It was attended by employees from the four corporate offices located in Mexico City.
Online training: “Intelligence and Prevention of Unlawful Transactions: Money Laundering, Fraud and Corruption” taught by PricewaterhouseCoopers to employees from specific departments that are responsible for risk prevention. Information sharing is divided into two stages. In the first stage, material is shared via e-mail to employees in the Marketing and Business Departments and in the Plant. In the second stage, it is shared via e-mail to employees in the Purchasing and Procurement Department.
- Reinforcing the Code of Ethics, targeting personnel from different departments This reinforcement takes place through one-hour, in-person training sessions.
- Course: “Practical Applications of the Code of Ethics for Public Accountants to Prevent Company Fraud” taught by the Instituto Mexicano de Expansión Fiscal y de Negocios, S.C., with the assistance of a Grupo Herdez employee.
203-1. Infrastructure investments and services supported
In 2018, we invested 199 million pesos (MXN) in new projects for the development and ongoing improvement of our plants and distribution centers.
SUMMARY OF MAIN PROJECTS | ||
COMPANY | PLANT/CEDIS | PROJECT TITLE |
Herdez | Cedis México | TI Order to Cash - Support Platform for Logistics Processes |
Alimentos Del Fuerte | Santa Rosa Tomate | Increase Capacity for Tomato Capture |
Herdez | Corporativo Cinco | Automation of Supply and Demand Planning Processes |
McCormick de México | SLP El Duque Mc | Substitution of the Filling and Capping Machine on Line 1 |
McCormick de México | SLP El Duque Mc | Increase capacity for Cappers 53, 63, and 70 MM |
Food Benefits | Commercial | Purchase Freezers and Trucks |
Food Benefits | Commercial | Purchase Freezers for Maintenance |
Nutrisa | Stores | Opening Owned Stores |
201-1. Direct economic value generated and distributed
Direct economic value generated: |
|
| 2018 |
Income + (cash flows) property sales + cash flows generated through financing activities | 20,970,682.93 |
Other Income (dividends received, interest charged, resources through sales of FA and royalties) | 1,041,068.00 |
Direct Economic Value Created (EVC): | 22,011,750.93 |
Operating Costs (cost of sales, increase in suppliers and increase in accounts payable) | 13,348,257.03 |
Salaries and social benefits for employees | 2,606,697.00 |
Payments to capital providers (dividends paid, interest paid, payments on long-term bank loans) | 3,149,759.00 |
Payments to Governments (Income Tax) | 998,614.34 |
Community investments | 54,051.70 |
Economic value distributed (EVD) | 20,157,379.07 |
Retained economic value (REV) | 1,854,371.86 |
405-2. Ratio of basic salary and remuneration of women to men
In accordance with our commitment to gender equality, and in alignment with the 5th Sustainable Development Goal, we calculate the ratio of base salary for women to men, which allows us to focus our efforts on closing the salary gap.
Mexico has gender pay gap of 34.2%, while at Grupo Herdez, the average does not surpass 6%.Job Category | Ratio of Basic Salary of Women to Men |
Operational | 78% |
Operational - Regulatory | 99% |
Tactical | 93% |
Strategic | 105% |
405-1. Diversity of governance bodies and employees
Governance Bodies | Women | Men | ||||
Less than 30 years of age | From 30 to 50 | More than 50 years of age | Less than 30 years of age | From 30 to 50 | More than 50 years of age | |
Board of Directors | - | 1 | 1 | - | - | 7 |
Audit Committee | - | - | - | - | - | 3 |
Business Practices Committee | - | - | - | - | - | 5 |
Risk Committee | - | 2 | - | - | 2 | 4 |
Energy Committee | - | - | - | - | 1 | 6 |
Ethics Subcommittee | - | 2 | - | - | - | 2 |
Breakdown of employees by gender
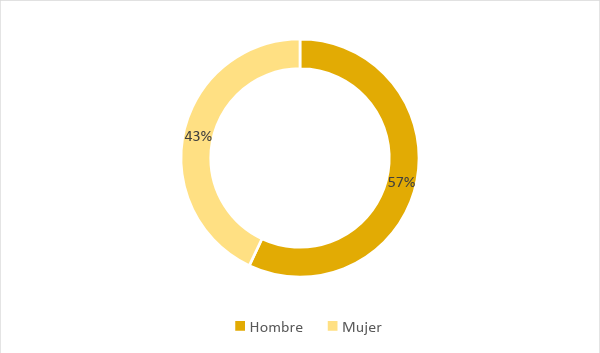
Breakdown of employees by job category
Men | Women | ||||
Year | Job Category | Total | Percentage (%) | Total | Percentage (%) |
2018 | Operational | 4,631 | 83% | 3,641 | 87% |
Operational-Regulatory | 780 | 14% | 484 | 12% | |
Tactical | 133 | 2% | 70 | 2% | |
Strategic | 21 | 0.38% | 2 | 0.05% | |
Total | 5,565 | 100% | 4197 | 100% |
Breakdown of employees by age group
| <30 | 30-50 | >50 | |||
Job Category | Total | Percentage (%) | Total | Percentage (%) | Total | Percentage (%) |
Operational | 3,736 | 92% | 3,840 | 79% | 696 | 82% |
Operational-Regulatory | 337 | 8% | 820 | 17% | 107 | 13% |
Tactical | 10 | 0.2% | 163 | 3% | 30 | 4% |
Strategic | 0 | 0% | 11 | 0.2% | 12 | 1.4% |
Total | 4,083 | 100% | 4,834 | 100% | 845 | 100% |
Job Category | Sex | Type of Disability | Age Range | Total |
Operational | Male | Motor disability | <30 | 1 |
404-3. Percentage of employees receiving regular performance and career development reviews
Out of our total workforce, 5,708 employees are non-unionized personell. We evaluated 38% of them on their work performance. Grupo Herdez does not have part-time personnel.
The performance and growth of our employees is evaluated at least once a year using different methodologies. These include 9-Box management by objectives, quarterly or four-month evaluations, and 360-degree feedback.
Unionized personnel are evaluated each month based on the production indices for the plant or distribution center where each employee works.
| Evaluated Employees | |||
| Full-Time | Part-Time | Total | |
Men | 1,324 | 0 | 1324 | |
Job Category | Operational | 576 | 0 |
|
Operational-Regulatory | 619 | 0 |
| |
Tactical | 121 | 0 |
| |
Strategic | 8 | 0 |
| |
| ||||
Women | 870 | 0 | 870 | |
Job Category | Operational | 427 | 0 |
|
Operational-Regulatory | 382 | 0 |
| |
Tactical | 59 | 0 |
| |
Strategic | 2 | 0 |
| |
Total | 2,194 |
404-2. Programs for upgrading employee skills and transition assistance programs
Grupo Herdez is aware that in order to achieve organic and continuous growth, it is essential to constantly develop the skills and aptitudes of our employees. Therefore, throughout the year we provide various training courses on different topics: technical expertise, values, health and safety, administration, environment, occupational health, 5’S, manufacturing practices, culture of legality, money laundering, fraud, corruption, and reinforcing the Code of Ethics.
In 2018, the training projects with the highest impact were the WCM efficiency program and the closure of the campaign to reinforce the Code of Ethics, which began in 2017 with 97 employees.Development Program | Description of Benefits to the Company | Quantitative Impacts (Monetary and Non-Monetary) | % of FTE Who Participated in the Program |
WCM Program (Plant Management Improvement) | - Achieve competitive costs- Boost productivity- Be the quality benchmark- Achieve world class management and operations- Obtain effective information systems | Plants: Lagos de Moreno, México, Barilla, El Duque, Chiapas, Industrias, Santa Rosa Tomates and Santa Rosa Vegetales Quantitative Impact:$58,187,922.86Qualitative Impact:- Loss reduction- Waste reduction- Optimized water consumption- Reduced risk premium- Efficiency control- Reduction in non-recoverable shrinkage- Identify opportunities for improvement in each pillar and each functional area. WCM management- Consolidate achievements with previous efforts and inject fresh methods into subsequent stages and challenges- Multidisciplinary teams- Generate floor training for employees to develop the implementation- Promote SDG as basis for the WCM model | 53% from plants |
Closure of the Reinforcement of the Code of Ethics | Program to reinforce employee adherence to the ethical principles espoused by Grupo Herdez. The purpose is to improve comprehension of the behaviors within the Code of Ethics through in-person sessions and visual support on dining hall screens, digital media, and printed material. | Qualitative Impact: Reinforcement of the culture of legality, values and ethical behavior within the different business units | 25% at the corporate offices, with a total of 97 employees |
Our Code of Ethics is available for viewing at https://grupoherdez.com.mx/conocenos/codigos-y-politicas/
Grupo Herdez does not have support programs for the transition period to lack of employment.
404-1. Average hours of training per year per employee
In 2018, our training budget was $15 million pesos, allowing us to teach a total of 158,058 hours, for an average of 16 hours per employee.
Total number of training hours | ||||
Year | Sex | Unionized | Non-Unionized | Total |
2018 | Men | 30,204.6 | 58,924.5 | 89,129.1 |
Women | 26,695.1 | 42,233.5 | 68,928.6 | |
Total | 158,058 |
Breakdown by gender (average hours)
Men | 28.4 |
Women | 37.7 |
Breakdown by type of contract (average hours)
Unionized | 42.3 |
Non-Unionized | 26.2 |
* Note: this period only provides data for man-hours by gender and type of contract, like the previous year. We do not report based on job category, since the reports received to date do not provide that type of information.
419-1. Non-compliance with laws and regulations in the social and economic areas
Grupo Herdez considers a significant fine to surpass or be equal to one million pesos. In 2018, there were no incidents of non-compliance with laws or regulations in the social and/or economic areas that generated significant fines.
401-2. Benefits provided to full-time employees that are not provided to temporary or part-time employees
The social benefits we offer to our employees are greater than those required by the Federal Labor Law (LFT) and are the same across all of the Companies within the Group.Social Benefits
Each employee is offered life insurance, public health services, disability or disablement coverage, parental leave, grocery vouchers and a pension fund. Insurance for major medical expenses is only offered to managers and directors.Through our Gender Equity Policy, we promote equality in our workforce. The salary for each category or vacancy is set regardless of gender.
This Policy may be viewed at https://grupoherdez.com.mx/sustentabilidad/codigos-y-politicas/
401-1. New employee hires and employee turnover
The following tables contain the new employee hires and employee turnover by age group, gender, and region for 2018:
New Hires
Women | ||||
| <30 | 30-50 | >50 | Total |
Corporate Office | 70 | 64 | 1 | 135 |
Plant | 140 | 104 | 22 | 266 |
Cedis | 1,153 | 121 | 8 | 1,282 |
Total | 1363 | 289 | 31 | 1683 |
|
|
|
|
|
Men | ||||
| <30 | 30-50 | >50 | Total |
Corporate Office | 121 | 103 | 4 | 228 |
Plant | 179 | 76 | 11 | 266 |
Cedis | 1,029 | 51 | 3 | 1,083 |
Total | 1329 | 230 | 18 | 1577 |
|
|
|
|
|
CEO | 3260 |
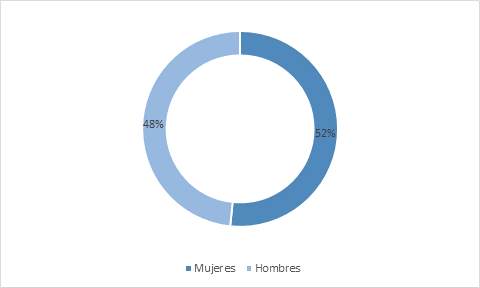
Attrition during the year
Women | ||||
| <30 | 30-50 | >50 | Total |
Corporate Office | 59 | 73 | 1 | 133 |
Plant | 155 | 133 | 32 | 320 |
Cedis | 1,735 | 268 | 21 | 2,024 |
Men | ||||
| <30 | 30-50 | >50 | Total |
Corporate Office | 76 | 174 | 22 | 272 |
Plant | 209 | 197 | 38 | 444 |
Cedis | 1,451 | 102 | 6 | 1,559 |
|
|
|
|
|
Grand Total | 3,685 | 947 | 120 | 4,752 |
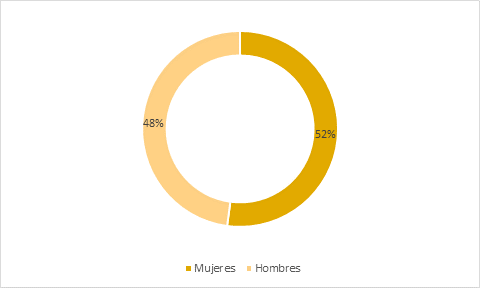
Turnover
Women | ||||
| <30 | 30-50 | >50 | Total |
Corporate Office | 23% | 15% | 2% | 17% |
Plant | 23% | 12% | 10% | 15% |
Cedis | 185% | 80% | 81% | 156% |
Total | 59% | |||
| ||||
Men | ||||
| <30 | 30-50 | >50 | Total |
Corporate Office | 18% | 13% | 13% | 14% |
Plant | 22% | 15% | 15% | 18% |
Cedis | 170% | 35% | 18% | 132% |
Total | 41% | |||
Grand Total | 49% |
102-55. GRI Content Index
The sustainability information was prepared in essential compliance with the Global Reporting Initiative (GRI) methodology in the GRI Standards version, Sustainable CPI indicators from the Mexican Stock Exchange, the principles of the United Nations Global Compact, and the Sustainable Development Goals issued by the United Nations Organization.
We report 117 contents, 10 of which are our own.
General Indicators | ||
Name | Contents | Description |
Strategy | 102-16 | Values, principles, standards, and norms of behavior |
Ethics and integrity | 102-17 | Mechanisms for advice and concerns about ethics |
102-18 | Governance structure | |
Corporate Governance | 102-19 | Delegating authority |
102-20 | Executive-level responsibility for economic, environmental and social topics | |
102-21 | Consulting stakeholders on economic, environmental and social topics | |
102-22 | Composition of the highest governance body and its committees | |
102-23 | Chair of the highest governance body and its committees | |
102-24 | Nominating and selecting the highest governance body | |
102-25 | Conflicts of Interest | |
102-26 | Role of highest governance body in setting goals, values and strategy | |
102-29 | Identifying and managing economic, environmental and social topics | |
102-31 | Review of economic, environmental and social topics | |
102-35 | Remuneration policies | |
102-36 | Process for determining remuneration | |
102-40 | List of stakeholder groups | |
Stakeholder engagement | 102-41 | Collective bargaining agreements |
102-42 | Identifying and selecting stakeholders | |
102-43 | Approach to stakeholder engagement | |
102-44 | Key topics and concerns raised | |
102-45 | Entities included in the consolidated financial statements | |
Corporate profile | 102-1 | Name of the organization |
102-10 | Significant changes to the organization and its supply chain | |
102-11 | Precautionary principle or approach | |
102-12 | External initiatives | |
102-13 | Memberships of associations | |
102-14 | Statement from senior decision maker | |
102-2 | Activities, brands, products and services | |
102-3 | Location of headquarters | |
102-4 | Location of operations | |
102-5 | Ownership and legal form | |
102-6 | Markets served | |
102-7 | Scale of the organization | |
102-8 | Information about employees and other workers | |
102-9 | Supply chain | |
Reporting practice | 102-46 | Defining report content and topic boundaries |
102-47 | List of material topics | |
102-48 | Restatements of information | |
102-49 | Changes in reporting | |
102-50 | Reporting period | |
102-51 | Date of most recent report | |
102-52 | Reporting cycle | |
102-53 | Contact point for questions regarding the report | |
102-54 | Claims of reporting in accordance with the GRI Standards | |
102-55 | GRI Content Index | |
102-56 | External assurance | |
Material Topics | ||
Name | Contents | Description |
Commitment and working environment | 103-12 | Management approach |
401-1 | New employee hires and employee turnover | |
401-2 | Benefits provided to full-time employees that are not provided to temporary or part-time employees | |
401-3 | Parental leave | |
404-1 | Average hours of training per year per employee | |
404-2 | Programs for upgrading employee skills and transition assistance programs | |
404-3 | Percentage of employees receiving regular performance and career development reviews | |
405-1 | Diversity of governance bodies and employees | |
405-2 | Ratio of basic salary and remuneration of women to men | |
406-1 | Incidents of discrimination and corrective actions taken | |
Business Development and Economic Performance | 103-7 | Management approach |
201-1 | Direct economic value generated and distributed | |
203-1 | Infrastructure investments and services supported | |
419-1 | Non-compliance with laws and regulations in the social and economic areas | |
Ethics and Anti-Corruption | 103-1 | Management approach |
205-1 | Operations assessed for risks related to corruption | |
205-2 | Communication and training about anti-corruption policies and procedures | |
205-3 | Confirmed incidents of corruption and actions taken | |
206-1 | Legal actions for anti-competitive behavior, anti-trust, and monopoly practices | |
415-1 | Political contributions | |
Environmental Management and Operational Efficiency | 103-13 | Management approach |
302-1 | Energy consumption within the organization | |
302-3 | Energy intensity | |
302-4 | Reduction of energy consumption | |
303-1 | Interactions with water as a shared resource | |
303-2 | Management of water discharge-related impacts | |
303-3 | Water withdrawal | |
303-4 | Water discharge | |
303-5 | Water consumption | |
305-1 | Direct (Scope 1) GHG emissions | |
305-2 | Other indirect (Scope 2) GHG emissions | |
305-4 | GHG emissions intensity | |
305-5 | Reduction of GHG emissions | |
305-6 | Emissions of ozone-depleting substances (ODS) | |
305-7 | Nitrogen oxides (NOx), sulfur oxides (SOx), and other significant air emissions | |
306-1 | Water discharge by quality and destination | |
306-2 | Waste by type and disposal method | |
308-1 | New suppliers that were screened using environmental criteria | |
IP-4 | Environmental investments | |
Supply Chain Management | 103-3 | Management approach |
204-1 | Proportion of spending on local suppliers | |
301-1 | Materials used by weight or volume | |
408-1 | Operations and suppliers at significant risk for incidents of child labor | |
409-1 | Operations and suppliers at significant risk for incidents of forced or compulsory labor | |
IP-6 | Agricultural Sustainability Program | |
Climate Change Risk | 201-2 | Financial implications and other risks and opportunities due to climate change |
Innovation in products and processes | 103-9 | Management approach |
IP-7 | Innovation management | |
IP-9 | Developing a Healthcare and Nutrition Strategy | |
Occupational Health and Safety | 103-11 | Management approach |
403-1 | Occupational health and safety management system | |
403-2 | Hazard and risk identification | |
403-3 | Occupational health services | |
403-4 | Worker participation, consultation, and communication on occupational health and safety | |
403-5 | Training on occupational health and safety | |
403-6 | Promotion of worker health | |
403-7 | Prevention and mitigation of occupational health and safety impacts | |
403-8 | Health and safety management system | |
IP-5 | Types and rates of injuries, occupational diseases, lost days, absenteeism, and work-related fatalities | |
IP-3 | Healthy food | |
Customer Health and Safety | 103-5 | Management approach |
416-1 | Assessment of the health and safety impacts of products or services | |
416-2 | Incidents of non-compliance concerning the health and safety impacts of products or services | |
417-1 | Requirements for product or service information and labeling | |
417-2 | Incidents of non-compliance concerning product or service information and labeling | |
417-3 | Incidents of non-compliance of non-compliance concerning marketing communications | |
IP-8 | Policies and practices to inform consumers | |
IP-1 | Customer and client relations | |
Community Engagement | DMA | Management approach |
IP-2 | Percentage of operations with implemented community engagement, impact assessments and development programs | |
IP-3 | Healthy and affordable food |
102-47. List of material topics
The following chart presents the limits (coverage) for each material topic:
| Material Topics | Boundaries (coverage) | |
|
| *Internal | **External |
High relevance | Ethics and Anti-Corruption | Grupo Herdez | Suppliers and contractors |
Risk management | Grupo Herdez | Suppliers (contractors) | |
Supply chain management | Manufacturing and marketing companies | Suppliers | |
Operational efficiency | Manufacturing and marketing companies | N/A | |
Consumer health | Manufacturing and marketing companies | Marketing and transport companies (Yes, third parties) | |
Medium relevance | Legal compliance | Grupo Herdez | N/A |
Business development | Grupo Herdez | Partner companies, financing institutions | |
Economic Performance | Grupo Herdez | N/A | |
Innovation (products and processes) | Manufacturing and marketing companies | Suppliers of raw materials, equipment and technology | |
Product labeling | Manufacturing companies | Authorities | |
Employee health and safety | Grupo Herdez | Contractors | |
Commitment and labor climate | Grupo Herdez | N/A | |
Environmental Management | Manufacturing companies | Agricultural and packaging suppliers |
*Internal limits: subsidiaries with a material aspect; i.e., where the impact is significant
**External limits: entities outside of the company, but linked to its activities, in which the aspect is material; i.e., where the impact is significant
102-9. Supply chain
We participate in a wide range of categories, including organic foods, tuna, burritos, ketchup, spices, guacamole, ice cream, mayonnaise, marmalade, honey, mole, mustard, pasta, tomato puree, home-style salsas, tea, and canned vegetables.
Our portfolio of exceptional brands includes Aires de Campo®, Barilla®, Búfalo®, Chi-Chi's®, Del Fuerte®, Don Miguel®, Doña María®, Embasa®, Helados Nestlé®, Herdez®, La Victoria®, McCormick®, Nutrisa®, Wholly Guacamole® and Yemina®.
In Mexico, we also have distribution agreements for Kikkoman®, Ocean Spray® and Reynolds®.
Grupo Herdez knows that the traceability of our raw materials and our relationship with our suppliers is essential to guaranteeing that our products reach our consumers’ tables with the quality we are known for. We have a diversified supply chain, without depending on any single supplier, that is sustained through two main focus areas: agricultural supply and strategic supply.
In the first type, the process for obtaining agricultural supplies of the highest quality is comprised of six stages:
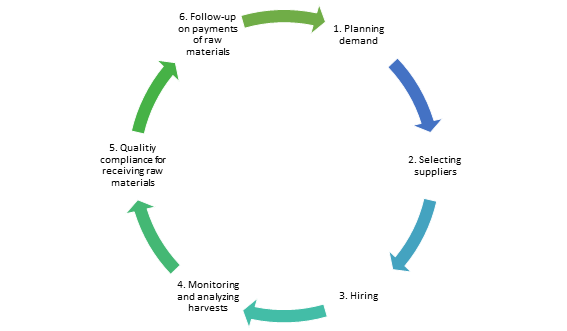
Our strategic supply process is comprised of 4 stages:
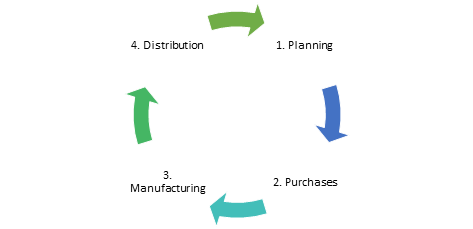
We have131 suppliers of agricultural raw materials, distributed throughout Mexico in the states of Aguascalientes, Baja California, Baja California Sur, Chihuahua, Mexico City, Durango, Guanajuato, Hidalgo, Morelos, Nayarit, Nuevo León, Puebla, San Luis Potosí, Sinaloa, Sonora and Zacatecas.
In 2018, the purchase of agricultural supplies required an investment of 823 million pesos. Likewise, we have 3,722 suppliers, of whom 1,793 are part of our supply chain, providing us with raw materials, packaging materials, machinery services and indirect services, for a value of more than 16,000 million pesos.
102-8. Information about employees and other workers
Breakdown of employees by employment contract
Year | Sex | Permanent | Temporary | Total |
2018 | Men | 4,712 | 853 | 5,565 |
Women | 3,604 | 593 | 4,197 | |
Total | 9,762 |
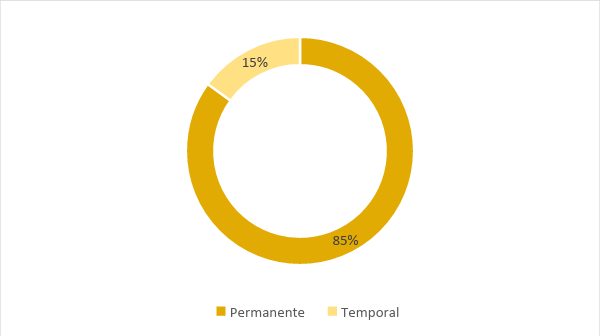
Breakdown of employees by region
Year | Region | Permanent | Temporary | Total |
2018 | Corporate Office | 2,498 | 168 | 2,666 |
Plant | 3,497 | 1,118 | 4,615 | |
Cedis | 2,321 | 160 | 2,481 | |
Total | 9,762 |
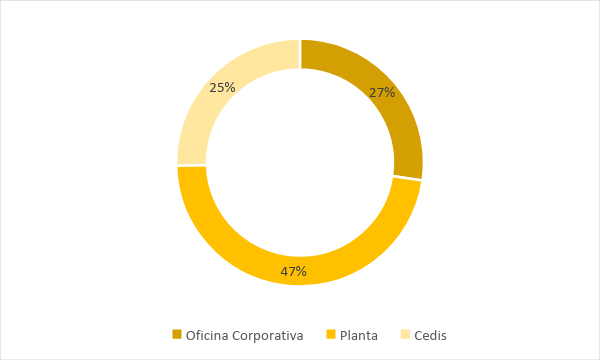
Grupo Herdez has sites with significant operations, including tuna vessels, distribution centers, offices, factories and Nutrisa® stores in Mexico.
The personnel on the tuna vessels is classified as plant staff and Nutrisa store personnel are classified within CEDIS.
Breakdown of employees by gender
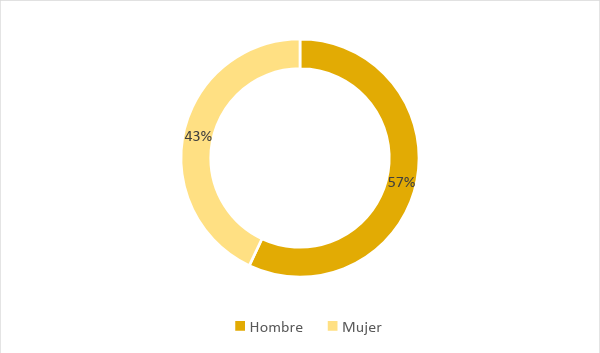
Year | Sex | Permanent | Temporary | Total |
2018 | Men | 4,712 | 853 | 5,565 |
Women | 3,604 | 593 | 4,197 | |
Total | 9,762 |
Year | Sex | Unionized | Non-Unionized | Total |
2018 | Men | 1,989 | 3,576 | 5,565 |
Women | 1,748 | 2,449 | 4,197 | |
Total |
|
| 9,762 |
We do not have part-time contracts. All employees, including those hired on a temporary basis, are directly hired by the company. We also do not have reduced workdays.
Likewise, in order to promote labor inclusion for persons with disabilities, this year Grupo Herdez joined part of the “Éntrale” alliance (driven by the Mexican Business Council), whose main objective is to create a culture of inclusion that will permit the integration of any person with a disability into our company. Currently, we have 1 person.
Job Category | Sex | Type of Disability | Age Range | Total |
Operational | Male | Motor disability | <30 | 1 |
102-45. Entities included in the consolidated financial statements
Grupo Herdez is structured as follows:
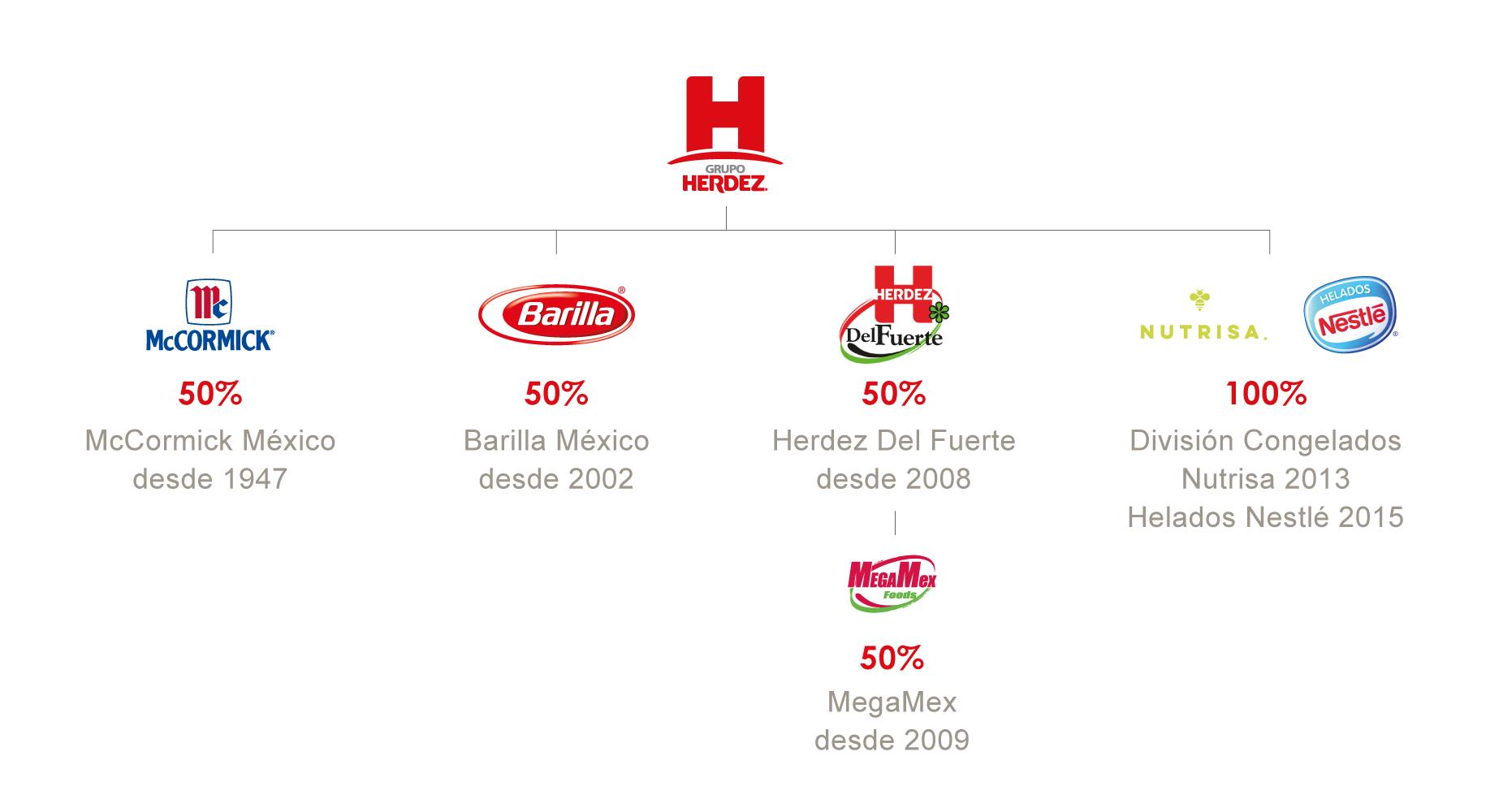
102-44. Key topics and concerns raised from stakeholder engagement
Stakeholder Group | Engagement Focus | Key Issues and Evaluation | Means of Communication | Engagement Frequency |
Shareholders | Interest with regard to the impact of environmental and social risks on the Company’s performance | Ongoing improvement of shareholder performance and sustainable | Annual Report | Annually |
Positioning the Group as a company that is committed to sustainable development | Website | Permanent | ||
Quarterly meetings | Quarterly | |||
Employees | Appropriate management of resources and supplies used in production processes | Establish a competitive standard in our employees, to generate talent development, trust, and dedication | Internal magazine Hechos con Amor [Made with Love] | Bimonthly |
Communication screens at all locations | ||||
Informative pamphlets | ||||
Implement training programs and development plans | Grupo Herdez University online platform | Permanent | ||
Printed and digital internal communication, with organizational and local coverage | ||||
Fundamental piece in the development of operations and achievement of objectives | Life programs that focus on improving well-being | Organizational climate survey and Herdez Man | Every three years | |
Benefits and business continuity | Training and awareness courses | Permanent | ||
Community | The Saber Nutrir® program focuses on improving nutritional conditions in Mexico. An important part of this movement is to improve the quality of life in the communities where we operate, which is why we implement projects that drive the local economy, improve nutrition habits and promote food security. | Diversify projects in communities to achieve food security, and to highlight its purpose. | Website sabernutrir.com.mx | Permanent |
Nutritional guidance for families through projects |
| |||
Ongoing monitoring of children with malnutrition | Quarterly operational report | |||
Consumers | To position Grupo Herdez as a sustainable company that is aware of its impact on the environment | Transparency in our environmental and social performance | Mass media and digital campaigns | Permanent |
Growing consumer interest in corporate sustainability practices, Company goals and objectives | Communicate the impact of our products within society and the environment | Website | ||
Growing consumer interest in environmentally friendly products | Share social projects that could help to generate value | Participate in various fora (conferences, workshops, etc.) | ||
Promote responsible consumption practices in our customers and end consumers | ||||
Suppliers | Promote appropriate procurement, exploitation and efficient use of resources to ensure operational sustainability | Comply with the certification of the Grupo Herdez quality and safety system, obtaining a grade above 80% | Questionnaire and feedback via e-mail | Permanent |
Obtain a performance evaluation (annual average) above 90% (quality, quantity and time) | Via e-mail |
102-43. Approach to stakeholder engagement
Stakeholder Group | Engagement Approach | Key Issues and Evaluation | Means of Communication | Frequency of Engagement |
Shareholders | Interest with regard to the impact of environmental and social risks on the Company’s performance | Ongoing improvement of shareholder performance and sustainable | Annual Report | Annually |
Positioning the Group as a company that is committed to sustainable development | Website | Permanent | ||
Quarterly meetings | Quarterly | |||
Employees | Appropriate management of resources and supplies used in production processes | Establish a competitive standard in our employees to generate talent development, trust, and dedication | Internal magazine Hechos con Amor [Made with Love] | Bimonthly |
Communication screens at all locations | ||||
Informative pamphlets | ||||
Implement training programs and development plans | Grupo Herdez University online platform | Permanent | ||
Printed and digital internal communication, with organizational and local coverage | ||||
Fundamental piece in the development of operations and achievement of objectives | Life programs that focus on improving well-being | Organizational climate survey and Herdez Man | Every three years | |
Benefits and business continuity | Training and awareness courses | Permanent | ||
Community | The Saber Nutrir® program focuses on improving nutritional conditions in Mexico. An important part of this movement is to improve the quality of life in the communities where we operate, which is why we implement projects that drive the local economy, improve nutrition habits and promote food security. | Diversify projects in communities to achieve food security and highlight its purpose | Website sabernutrir.com.mx | Permanent |
Nutritional guidance for families through projects |
| |||
Ongoing monitoring of children with malnutrition | Quarterly operational report | |||
Consumers | To position Grupo Herdez as a sustainable company that is aware of its impact on the environment | Transparency in our environmental and social performance | Mass media and digital campaigns | Permanent |
Growing consumer interest in corporate sustainability practices, Company goals and objectives | Communicate the impact of our products within society and the environment | Website | ||
Growing consumer interest in environmentally friendly products | Share social projects that could help to generate value | Participate in various fora (conferences, workshops, etc.) | ||
Promote responsible consumption practices in our customers and end consumers | ||||
Suppliers | Promote appropriate procurement, exploitation and efficient use of resources to ensure operational sustainability | Comply with the certification of the Grupo Herdez quality and safety system, obtaining a grade above 80% | Questionnaire and feedback via e-mail | Permanent |
Obtain a performance evaluation (annual average) above 90% (quality, quantity and time) | Via e-mail |
102-41. Percentage of employees covered by collective agreements
Besides promoting labor inclusion, we also respect the right to collective bargaining. Of our 9,762 employees, 38% are part of a collective agreement, the same percentage as the previous year.
Total Employees: 9,762 employees.
Number of employees per collective agreement | Number of non-unionized employees |
3,737 | 6,025 |
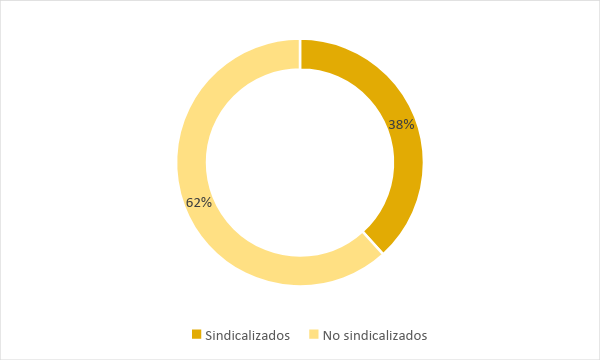
102-40. Stakeholders
Producing long-term, mutually beneficial relationships with our employees, consumers, shareholders, communities, internal suppliers and the government, is essential to ensuring the success and transcendence of our business, environmental, and economic strategies and objectives.
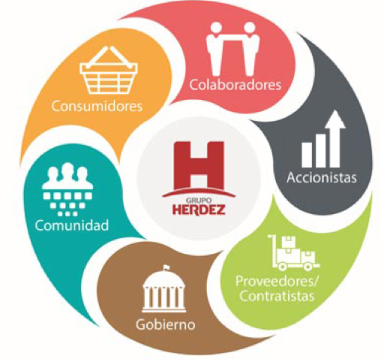
102-22. Composition of the supreme governing body and its committees
In 2018, an independent advisor and member of the Audit Committee left the company and a female independent advisor joined the Company.Governance Bodies | Women | Men | ||||
Less than 30 years of age | From 30 to 50 | More than 50 years of age | Less than 30 years of age | From 30 to 50 | More than 50 years of age | |
Board of Directors | - | 1 | 1 | - | - | 7 |
Audit Committee | - | - | - | - | - | 3 |
Business Practices Committee | - | - | - | - | - | 5 |
Risk Committee | - | 2 | - | - | 2 | 4 |
Energy Committee | - | - | - | - | 1 | 7 |
Ethics Subcommittee | - | 2 | - | - | - | 2 |
Governance Bodies | |
Intermediaries | Internal |
Audit Committee | Risk Committee |
3 Advisors | 8 members |
(100% independent) | |
Business Practices Committee | Ethics Subcommittee |
5 Advisors | 4 members |
(60% independent) | |
| Energy Committee |
| 7 members |
Héctor Hernández-Pons Torres
Chairman of the Board of Directors
CEO
Graduate of the Faculty of Law at Universidad Anáhuac and from the National University in San Diego, CA, where he studied a Master of Business Administration. He started working in Herdez in 1978 in the Legal Department and since then, has held various positions throughout the Company. In 2004, he was appointed Chairman of the Board of Directors and CEO of Grupo Herdez.
In addition to his responsabilities within the Group, he has served in several organizations, including Regional Advisor to Banamex and Nacional Financiera, Vice President of Concamín, Chairman of the Board of Directors for the Papalote Children’s Museum and of the National Chamber of the Canned Food Products Industry (CANAINCA). Currently, he serves as the President of the Herdez Foundation, Advisor to the Papalote Children’s Museum, and participates as a Trustee on the Mexican Business Council, and on the Communication Council.
Enrique Hernández-Pons Torres
Vice-Chairman of the Board of Directors
Deputy CEO
Bachelor of Business Administration with graduate studies abroad in Marketing and Business Management. He has worked at Grupo Herdez since 1971 in various departments and positions, including Sales, Marketing, Accounting and other areas, and currently serves as the Vice-Chairman of the Board and Deputy CEO for Grupo Herdez, and Chairman of the Board at MegaMex in the United States.
Enrique Castillo Sánchez Mejorada
Independent Advisor
Bachelor of Business Administration. He began his professional career at Banco Nacional de México. He held various executive positions in Mexico in Nacional Financiera, Casa de Bolsa Inverlat, Seguros América, Inverméxico/Banco Mexicano, Credit Suisse México, and he served as Chairman of the Board of IXE Grupo Financiero. He was also Vice Chairman and President of the Mexican Banks Association. Currently he serves as Chairman of the Board of Directors of MaxCom Telecomunicaciones, S.A.B. de C.V., and Non-Executive Chairman of the Board of Directors of Banco Nacional de México. He is a Member of the Board of Directors for Grupo Alfa, S.A.B de C.V., Southern Copper Corporation, and Médica Sur, S.A.B. de C.V.
Eduardo Ortiz Tirado Serrano
Independent Advisor
Bachelor of Business Administration from Universidad Anáhuac. He began his professional career in Herdez, where he worked in the Marketing Department. Later he moved to marketing at Richardson Vicks and Procter & Gamble for six years. In 1988 he began at SC Johnson and Son, S.A. de C.V., as Director of Marketing. In 1992, he participated in a sales training program in Los Angeles, California, as an International Associate . In 1993, he returned to Mexico as Sales Director of SC Johnson Mexico and in 1995, he was promoted to CEO of SC Johnson for Mexico and Central America. In 2001, he was named Corporate Vice-President and CEO for Mexico and Central America. In January 2013, he retired from SC Johnson. He served as Advisor to the Council for Self-Regulation and Advertising Ethics (CONAR), Advisor to the Mexican Center for Philanthropy (CEMEFI), and the Advisory Council to Great Place To Work Mexico. Currently, he serves as the CEO for Grupo Zapata, Advisor to Herdez, and is a member of the Audit Committee. He is also an Advisor to the Mañana para la Comunidad Foundation and a member of the Advisory Council to the Xochitla Foundation.
José Roberto Danel Díaz
Independent Advisor
Public Accountant, a graduate of Universidad Iberoamericana. He completed graduate studies in Administration at the Instituto Tecnológico Autónomo de México (ITAM); in Senior Managment at the Pan-American Institute for Senior Business Management (IPADE); in Corporate Governance at the Yale School of Management, at the Stanford Graduate School of Business and at the Harvard Business School.
Chairman of the Corporate Governance Best Practices Committee for the Business Coordination Council; Member of the Latin American Roundtable on Corporate Governance (OECD-World Bank), the National Association of Corporate Directors (USA), the International Corporate Governance Network (UK) and of its Risk Committee.
José Manuel Rincón Gallardo
Independent Advisor
Public Accountant, a graduate of the Universidad Nacional Autónoma de Mexico (UNAM). Completed various courses at universities in the United States and Europe. He is a member of the Mexican Institute of Public Accountants, the Mexican Institute of Financial Executives, the Corporate Governance Committee of the Business Coordination Council, a founding member of the Mexican Council for Research and Development of Financial Information Standards (CINIF). He was a managing partner of KPMG México, a member of the firm’s International Council, President for Latin America and a Member of the United States Council. Currently, he serves as an Independent Advisor to Cementos Mexicanos, Cinépolis, Citelis, Sonoco Operadora, Grupo Invekra, Peña Verde, Quálitas Compañía de Seguros, Grupo CP and Fondo WAMEX.
Luis Rebollar Corona
Independent Advisor
A Chemical Engineer, he is a graduate of the Universidad Nacional Autónoma de México (UNAM), and has served as CEO for Fábrica de Papel San Rafael, Cia. Industrial de San Cristóbal, Alcatel, Sidek and Situr. He also served as an Advisor and Chairman at Sidek and Situr. Currently, he is an Advisor to Grupo Gigante, Grupo Sánchez and Grupo Industrial Mexicano. He participated in the restructuring of Satélites Mexicanos, serving as the Chairman of its Board. For 18 years, he was Chairman of the Board of Sandvik de México.
Anasofía Sánchez Juárez Cardoze
Independent Advisor
With a Bachelor’s in Marketing from the Tecnológico de Monterrey, she has a Master’s in Communication, Advertising and New Media from the Institut des hautes études économiques et commerciales (INSEEC), in France. She also studied at HEC Paris and at The Wharton School in Philadelphia. She is a professor in the Master Internet Business program at the Higher Institute for Internet Development (ISDI). Currently, she serves as the CEO at Waze México. Prior to joining Waze, she was the Business Director for Mexico and Central America at Facebook, a position she held for more than five years. Previously, she served as the Brand Solutions Manager for Google and was the Business Leader for YouTube México.
102-18. Corporate Governance Structure and Committees
Governance Bodies | Women | Men | ||||
Less than 30 years of age | From 30 to 50 | More than 50 years of age | Less than 30 years of age | From 30 to 50 | More than 50 years of age | |
Board of Directors | - | 1 | 1 | - | - | 7 |
Audit Committee | - | - | - | - | - | 3 |
Business Practices Committee | - | - | - | - | - | 5 |
Risk Committee | - | 2 | - | - | 2 | 4 |
Energy Committee | - | - | - | - | 1 | 7 |
Ethics Subcommittee | - | 2 | - | - | - | 2 |
Committee Duties | |
Committee | Duties |
Audit Committee | Provide support, opinions and advice regarding the guidelines on internal audit and control, accounting policies, financial statements, hiring external auditors, risks that the Company is exposed to, policies on information and communication with shareholders and the market. |
Business Practices Committee | Provide opinions about the policies and guidelines governing the use or enjoyment of the goods that make up the Company’s assets, the transactions that the Company will undertake, naming and selecting the Chief Executive Officer, policies for granting loans, borrowing, or credits; waivers in order to take advantage of business opportunities; supporting the Board of Directors in developing the activities listed in Article 42 of the Stock Market Act and those listed in the Code of Best Corporate Practices. |
Risk Committee | Identify the risks that affect the achievement of the objectives within the area(s) under its responsibility; measure, analyze and monitor them; formulate appropriate response mechanisms (controls) for the identified risks and implement them efficiently; establish guidelines for reporting to the Risk Committee. |
Energy Committee | Establish energy goals, perform diagnostics on energy efficiency, the viability of clean energy, implement Energy for Preserves (EPC) projects, and produce an Energy Master Plan. |
Ethics Subcommittee | Produce guidelines and directives for ethical behavior; contribute to the ethical management of the Company through standards documents (policies and procedures); address controversies related to appreciation, conflicts of interest and behavior between stakeholders. |
Governance Bodies | |
Intermediaries | Internal |
Audit Committee | Risk Committee |
3 Advisors | 8 members |
(100% independent) | |
Business Practices Committee | Ethics Subcommittee |
5 Advisors | 4 members |
(60% independent) | |
| Energy Committee |
| 8 members |